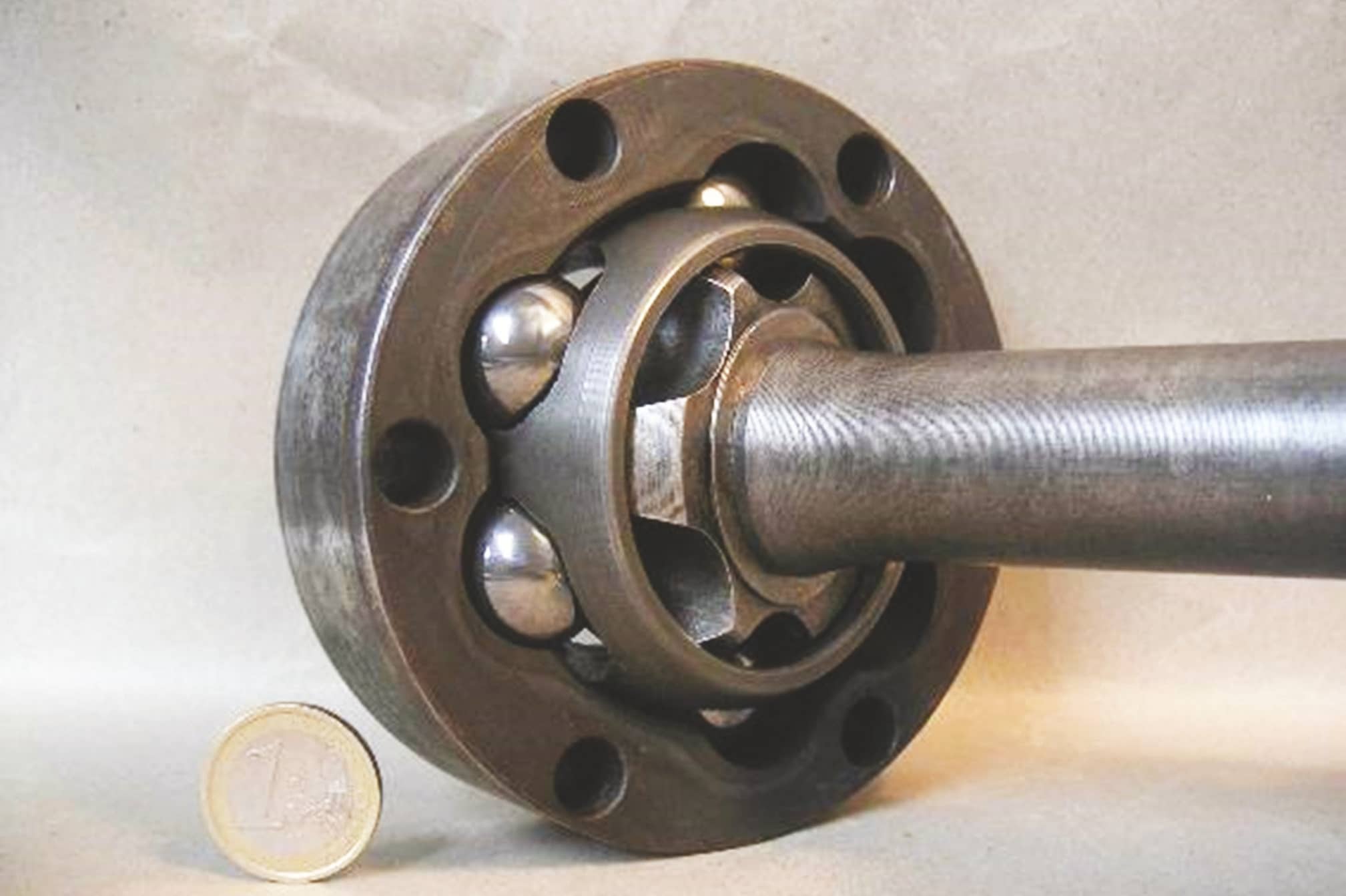
Ball cages are used in vehicle CV joints.
Source: Wikimedia Commons / Wikipedia entry “Homokinetisches Gelenk”
“Ball cages are made in over 80 different versions. Automobile manufacturers often outsource variants with low unit quantities and lot sizes to suppliers,” says Robert Keller, Director of Stamping Technology at Karl Klink GmbH. That presents a great challenge to these companies .“For one thing, these suppliers have to do tool changes, significantly lowering machine availability and rising costs,” reports Keller .“For another, the flywheel drive used so far by most punching machines results in fixed slide kinematics, yielding in relatively low cut quality and output .”
The problem was brought to the attention of Karl Klink GmbH by discussions with an automotive supplier at the Blechexpo fair in Stuttgart a few years ago. Based on this feedback, the company developed a high-performance automatic ball cage punching machine that meets users’ advanced requirements for high cut quality and shorter retooling times.
Ball cages come in many different varieties. They differ in shape, size, and number of windows.
The RT-HLKK1000 automatic punching machine launched recently is based on the prototype presented in 2015, but with many new improvements. The power source sets the Klink machine apart. Instead of a flywheel, it uses a servo drive which improves the cut surface quality by increasing the cutting speed. Thus, it has been possible to combine higher quality with higher productivity.
هذه القصة مأخوذة من طبعة January - February 2021 من Forgings Today.
ابدأ النسخة التجريبية المجانية من Magzter GOLD لمدة 7 أيام للوصول إلى آلاف القصص المتميزة المنسقة وأكثر من 9,000 مجلة وصحيفة.
بالفعل مشترك ? تسجيل الدخول
هذه القصة مأخوذة من طبعة January - February 2021 من Forgings Today.
ابدأ النسخة التجريبية المجانية من Magzter GOLD لمدة 7 أيام للوصول إلى آلاف القصص المتميزة المنسقة وأكثر من 9,000 مجلة وصحيفة.
بالفعل مشترك? تسجيل الدخول
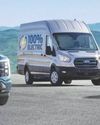
Ford To Manufacture Batteries For Its Future Electric Vehicles
Ford and SK Innovation have signed a MoU to create a joint venture, to be called BlueOvalSK, to produce approximately 60 GWh annually in traction battery cells and array modules, starting mid-decade, with the potential to expand.
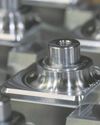
Modern technology has revolutionized aluminium forging
More than 150 years ago, Danish chemist Hans-Christian first successfully extracted aluminium from ore. At the time, the intricacies of the extraction process made aluminium a truly precious commodity.
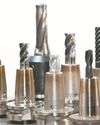
Italian machine tool industry registers significant growth
During the first quarter of 2021, demand for Italian machine tools grew again. The UCIMU index processed by the Economic Studies Department & Business Culture of the Association showed a 48.6 % upturn in the first three months of the year compared with the same period of 2020.
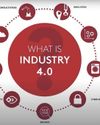
Industry 4.0 - Concept of Manufacturing
Industry 4.0 refers to the concept of manufacturing where machines are augmented with wired or wireless connectivity and sensors, connected to a system that has capability to visualise the entire production line and make decisions.

Bharat Forge to set up new factory for defence business
Bharat Forge is looking to acquire 175 acres in an industrial park near Pune for Rs 240 crore which will house new factories for its defence and electric mobility business divisions.
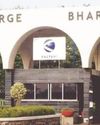
Bharat Forge identifies two new growth drivers
Pune-based forging giant Bharat Forge has charted a course involving two new growth drivers over the next five years, involving electric vehicles (EV) and light-weighting technologies for automobiles.
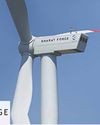
Bharat Forge acquires Nouveau for Sanghvi Forgings acquisition
Forging company Bharat Forge (BFL) announced the acquisition of 100% stake in Nouveau Power & Infrastructure, a group company 100% owned by promoters of BFL.
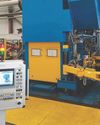
Fully automatic closed-die forging line from SMS
Chinese automotive supplier Ningbo Xusheng Auto Technology Co., Ltd. has issued the Final Acceptance Certificate to SMS group for the new, fully automatic closed-die forging line installed at the company’s Ningbo location in the Chinese province of Zhejiang.
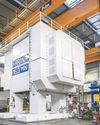
16 000 ton press presented for the first time
Schuler and its affiliate Farina have demonstrated the world’s largest mechanical forging line to an international group of 60 forging experts. A live video stream transmitted from the production site in Suello close to Milano showed the impressive features of the 16 000 ton press with a stroke of 600 mm in action. It will be delivered to the German company ThyssenKrupp Gerlach.
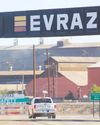
Making Steel With Solar Energy
EVRAZ North America plans construction of a long-rail mill at its Rocky Mountain Steel operation in Pueblo, Colo. This decision allows execution of an agreement for a 240-megawattsolar facility located on 1,500 acres of land at the steel mill.