Large Furnaces Shaping Refractory Future
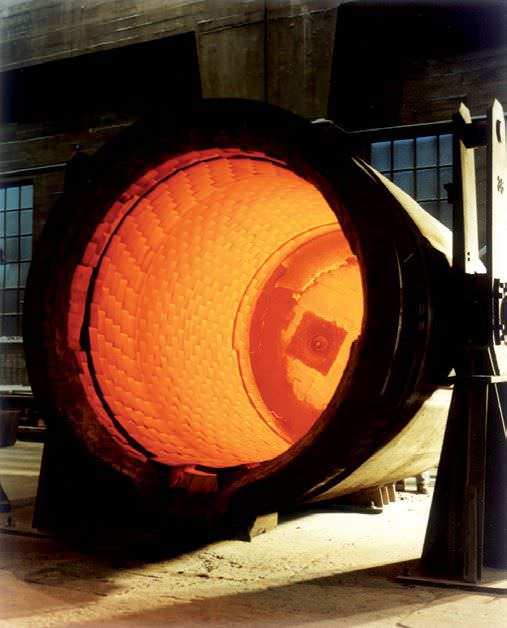
The refractory industry in India is undergoing changes. And the reasons for the transition in demand are three-fold – increase in the capacity of furnaces; shift in technology or operational philosophy and demand for new grades and improved quality of steel.
Nowadays, to gain from economies of scale, user industries of refractories, mainly the steel industry, which commands a leading 70-75 percent share of the demand, are opting for larger capacity furnaces. Today, blast furnaces in steel plants with a working volume of more than 4,000 m3 and basic oxygen furnaces of 300 tons are the order of the day. And to support these kinds of hugely productive furnaces, there is a need for technically improved refractory materials, which is being met by the industry, resulting in a gradually reducing demand for the conventional refractory.
Innovations
Refractory materials are used in providing refractory lining in furnaces, kilns, incinerators, and reactors. These materials have a high melting point (greater than 1,520 degree Celsius) and they are subjected to various conditions such as extremely high temperature, abrasions and chemical corrosions, slag attacks and chemical reactions when they are used in refractory linings. Hence, these materials must be able to endure these conditions with less wear and tear and high reliability.
In a bid to satisfy the demand for highly efficient refractory requirements of the steel industry, the refractory makers are resorting to innovations.
هذه القصة مأخوذة من طبعة December 2017 من Steel Insights.
ابدأ النسخة التجريبية المجانية من Magzter GOLD لمدة 7 أيام للوصول إلى آلاف القصص المتميزة المنسقة وأكثر من 9,000 مجلة وصحيفة.
بالفعل مشترك ? تسجيل الدخول
هذه القصة مأخوذة من طبعة December 2017 من Steel Insights.
ابدأ النسخة التجريبية المجانية من Magzter GOLD لمدة 7 أيام للوصول إلى آلاف القصص المتميزة المنسقة وأكثر من 9,000 مجلة وصحيفة.
بالفعل مشترك? تسجيل الدخول
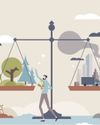
Steel's Net Zero mission
The country’s commitment to achieving Net Zero within a targeted timeframe will now propel its steel sector towards a sustainable future in line with global trends.
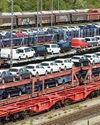
Fuel Price Hike, Supply Chain Disruption Hurt Festive Sales
Supply chain disruptions and fuel price hikes have hurt festive sales in a big way as most auto majors posted decline in sales in October.
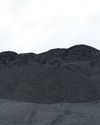
Seaborne coking coal offers remain range-bound
Seaborne coking coal offers moved in a narrow range in October amid global supply tightness and healthy spot demand.
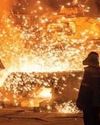
Global crude steel output down 8% in September
China manufactured 74 mt in September, fall of 21% y-o-y while India’s production went up by 7% to 10 mt.
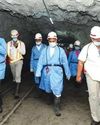
MOIL embarks on expansion projects
“Even though our country is blessed with manganese ore reserves, we import 50% of the domestic requirement. We have to lower our import dependence and save precious foreign exchange.” Ram Chandra Prasad Singh, Steel Minister
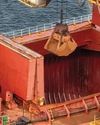
Iron ore handled by major ports down 17% in H1
The 12 major Indian ports handled 27 mt of iron-ore during H1 of 2021, down by 17% from 33 mt recorded for the corresponding period of previous year.
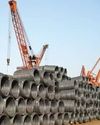
Shrinking China output to boost India exports
“In the third quarter of 2021, the company actively responded to the pressure from external policies, such as production curtailment and dual control system on energy consumption and intensity, as well as coal resource shortage and surging prices.” Baoshan Iron and Steel Co Ltd
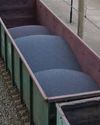
Indian Railways' iron-ore handling up 25% in H1
Indian Railways in April-September of 2021 (H1) transported 84 mt of iron ore, up by 25% over 67 mt during April-September 2020.
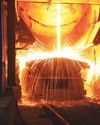
September crude steel production up 7.2% y-o-y
India’s crude steel production in September 2021 grew 7.2 percent to 9.547 million tons (mt) over September 2020 but was down by 3.2 percent from August 2021 output, provisional steel ministry data showed.
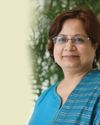
“Five enablers: way forward to sustainable cleaner steel”
Right and scalable technology, appropriate policy guidance by government, access to finance to fund transition, willingness of customers to pay for cleaner products and infrastructure for use of new technologies are the need of the hour for the sustainable and cleaner steel industry, according to Madhulika Sharma, Chief Corporate Sustainability, Tata Steel.