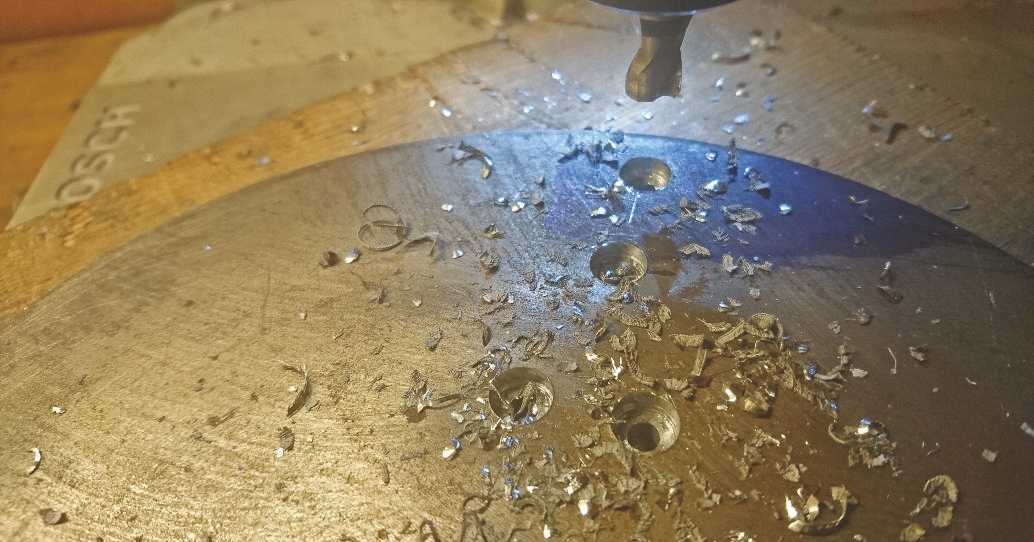
To finish the plates, they were drilled, again on the bench mill, photo 62Next part I made was the plate that fixes the saw cutting blade, this I call “scroll saw arm”, fig. 12.
This part was made from 3.0mm mild steel sheet and the first job was to mark out the outer shape according to the figure, photo 64.
Next, the part was roughly cut out using my band saw, photo 65. Finally, the edge was filed smooth, photo 66 to finish the arm.
The 4.5mm holes where drilled in the bench drill, photo 67 and the oblong 4.5 x 8.5 slot was made using a round file.
Next part I made was the bracket that should hold the saw cutting blade at the upper end, fig 13.
This part was made from a piece of 14 x 14mm hot rolled steel, and after cutting a blank a little over size according to the figure, all sides was milled to final dimension as per the figure, photo 68.
Next the M4 holes were drilled and tapped, photo 69.
As the idea with this tool is that it can be used as a scroll saw and a filing machine, I’ve designed it with interchangeable support for the work pieces that are to be worked on. Therefore, the next part I made was a support button for the scroll saw application, fig 14.
In fact, I made a set of buttons so these later could be adapted to appropriate jobs.
The buttons were made from 40mm mild steel, and after cutting the discs a little wider than the final measure, photo 73, they where faced off to final thickness of 5mm, photo 75.
Next the discs were placed onto the bench mill and the two 2.5mm counter bored holes were made, photo 76.
هذه القصة مأخوذة من طبعة December 2019 من Model Engineers' Workshop.
ابدأ النسخة التجريبية المجانية من Magzter GOLD لمدة 7 أيام للوصول إلى آلاف القصص المتميزة المنسقة وأكثر من 9,000 مجلة وصحيفة.
بالفعل مشترك ? تسجيل الدخول
هذه القصة مأخوذة من طبعة December 2019 من Model Engineers' Workshop.
ابدأ النسخة التجريبية المجانية من Magzter GOLD لمدة 7 أيام للوصول إلى آلاف القصص المتميزة المنسقة وأكثر من 9,000 مجلة وصحيفة.
بالفعل مشترك? تسجيل الدخول

Readers' Workshops - Patrick Cubbon
Patrick Cubbon describes his workshops – a portable one from 1963 and the current accommodation

Desktop Gear Hobbing
Toby Kinsey has designed this fascinating piece of gearmaking equipment

The John Stevenson Trophy 2020
Many readers and forum members will remember John Stevenson, a contributor to MEW but best known for his larger-than life presence on the Model Engineer forum.

From the Archives: Twist drill Sharpening by the Four Facet Method
Giles Parkes, MEW Issue 64, February/March 2000

Dividing on the Warco 220 Lathe
Peter Shaw describes a mandrel dividing attachment for this popular lathe that can be adapted to fit many other benchtop machines

Choosing Steels
Stub Mandrel offers some advice on choosing the right steel for the job

A Storage Story
Robin King shares the lessons learned from his experience of workshop moves

A Simple Drill Grinding Aid
A newcomer to our hobby was having trouble sharpening drills, so Howard Lewis made a simple aid for him

Yet Another Bodge-Up!
Peter Shaw finds a use for some aged homebrew slot drills.

Workshop Press Tooling Part 2
Will Doggett makes a set of tooling for his press tool described starting in issue 285