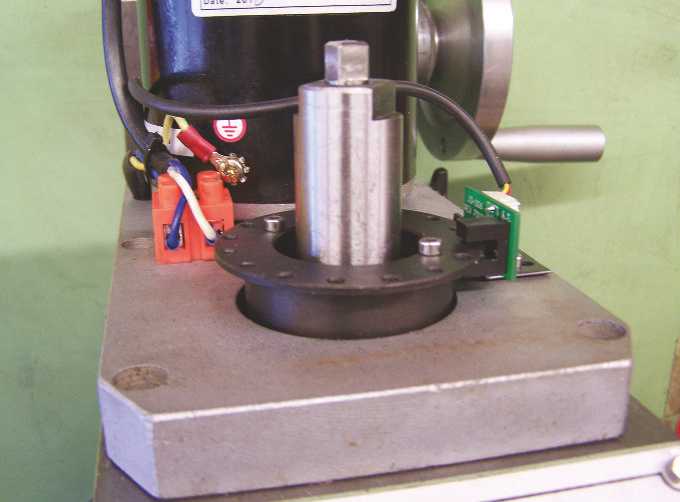
Introduction
I was starting to make a drill sharpening jig which required a slot to be milled at a precise angle, so I set up a pair of toolmaker’s buttons on the mill table to use a sine-bar to set the angle. When I came to use the dial indicator to set the buttons parallel to the table, I realised that holding the dial indicator in the spindle required that the spindle had to be prevented from rotating in order to be able to obtain a satisfactory reading. This required a lot of head scratching and thinking as to how I could build a spindle hold without altering the machine itself.
I hesitated to call this a spindle lock, as that would suggest that the spindle was well and truly locked and should allow quite a bit of torque to be used. This is not the case – it merely serves to hold the spindle from rotating whilst the DTI is used. Similarly, I did not call it a spindle brake, as this might imply a method of bringing the spindle to a stop whilst it is rotating, so I decided to call it a spindle hold.
My first and primary objective was to make it such that no alterations were made to the milling machine at all. I found that I could not achieve this objective fully, as I did end up having to drill an access hole for the screw to operate the spindle hold. I considered that a single 7mm diameter hole in the plastic cover over the motor and spindle was acceptable. Otherwise, there are no irreversible alterations to the milling machine.
هذه القصة مأخوذة من طبعة December 2019 من Model Engineers' Workshop.
ابدأ النسخة التجريبية المجانية من Magzter GOLD لمدة 7 أيام للوصول إلى آلاف القصص المتميزة المنسقة وأكثر من 9,000 مجلة وصحيفة.
بالفعل مشترك ? تسجيل الدخول
هذه القصة مأخوذة من طبعة December 2019 من Model Engineers' Workshop.
ابدأ النسخة التجريبية المجانية من Magzter GOLD لمدة 7 أيام للوصول إلى آلاف القصص المتميزة المنسقة وأكثر من 9,000 مجلة وصحيفة.
بالفعل مشترك? تسجيل الدخول

Readers' Workshops - Patrick Cubbon
Patrick Cubbon describes his workshops – a portable one from 1963 and the current accommodation

Desktop Gear Hobbing
Toby Kinsey has designed this fascinating piece of gearmaking equipment

The John Stevenson Trophy 2020
Many readers and forum members will remember John Stevenson, a contributor to MEW but best known for his larger-than life presence on the Model Engineer forum.

From the Archives: Twist drill Sharpening by the Four Facet Method
Giles Parkes, MEW Issue 64, February/March 2000

Dividing on the Warco 220 Lathe
Peter Shaw describes a mandrel dividing attachment for this popular lathe that can be adapted to fit many other benchtop machines

Choosing Steels
Stub Mandrel offers some advice on choosing the right steel for the job

A Storage Story
Robin King shares the lessons learned from his experience of workshop moves

A Simple Drill Grinding Aid
A newcomer to our hobby was having trouble sharpening drills, so Howard Lewis made a simple aid for him

Yet Another Bodge-Up!
Peter Shaw finds a use for some aged homebrew slot drills.

Workshop Press Tooling Part 2
Will Doggett makes a set of tooling for his press tool described starting in issue 285