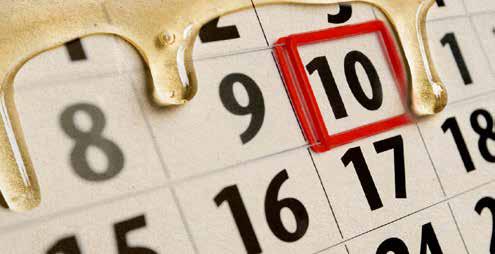
Potential consequences run the gamut, from subtle issues like increased operating temperature, to more severe issues like machine frothing, total machine failure or permanent structural damage to the equipment. In "System Approach to Contamination Control," Vickers, Inc., found that "proper selection and placement of contamination control devices... eliminates (the root cause of) up to 80% of hydraulic system failures."
In fact, Bearing Maintenance Handbook, SKF, states that proper lubrication and ideal conditions could theoretically result in "infinite life" for bearings, meaning that the sky is the limit in the potential benefits of lubricant improvement. And aside from the obvious lost uptime, this can also result in expensive product integrity investigations to rigorously stress-test the entire work flow.
One factor exacerbating the problem is that early signs of lubricant contamination are so subtle and diverse that they’re often over looked by hard working crews. But even if these issues never culminate in the worstcase scenario, the aggregate wear and loss of efficiency over an extended period — and spread across a fleet of machines — can still result in a massive impact on revenue and production scheduling.
While regularly scheduled lubricant-replacement routines are the standard solution to this challenge, modern innovations have made it possible to achieve higher levels of efficiency, reliability and cost-effectiveness with an oil-analysis routine. Such a routine is more adaptive to the specifics of your project and can save compounding amounts of time and money by extending uptime and reducing maintenance costs throughout your equipment.
Causes of Lubricant Contamination
هذه القصة مأخوذة من طبعة March - April 2024 من MACHINERY LUBRICATION INDIA.
ابدأ النسخة التجريبية المجانية من Magzter GOLD لمدة 7 أيام للوصول إلى آلاف القصص المتميزة المنسقة وأكثر من 9,000 مجلة وصحيفة.
بالفعل مشترك ? تسجيل الدخول
هذه القصة مأخوذة من طبعة March - April 2024 من MACHINERY LUBRICATION INDIA.
ابدأ النسخة التجريبية المجانية من Magzter GOLD لمدة 7 أيام للوصول إلى آلاف القصص المتميزة المنسقة وأكثر من 9,000 مجلة وصحيفة.
بالفعل مشترك? تسجيل الدخول
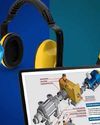
KEY CONSIDERATIONS IN INDUSTRIAL LUBRICATION FOR ENHANCED WORK PLACE SAFETY
Insufficient attention to every day industrial lubrication tasks can compromise safety and lead to costly breakdowns.
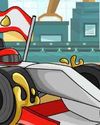
GREASING THE WHEELS OF SUCCESS: A ROADMAP TO LUBRICATION EXCELLENCE
Yup, it's 2025 already! And it goes without saying that maintaining machinery at peak-performance is not just a goal but a necessity.
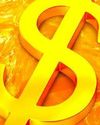
THE RISING VALUE OF CALCIUM SULFONATE COMPLEX GREASE IN MACHINERY RELIABILITY
Lubricant choice has a large impact on machinery reliability. Maintnance engineers have many options when selecting the proper grease for their machinery.
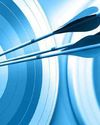
OPTIMIZE YOUR MAINTENANCE SUCCESSJOURNEY WITH QUICK WINS
This article is a crossover from Machinery Lubrication's sister publication, Reliable Plant.
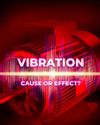
VIBRATION CAUSE OR EFFECT?
The understanding of machinery vibration analysis often leads to confusion regarding whether vibration is the cause of a problem, the result of a problem, or both.
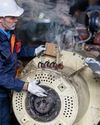
THE PERILS OF IGNORING LOW OR FLUCTUATING OIL LEVELS
I've seen people shrug off the importance of fluctuating oil levels when they inspect sightglasses.
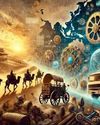
FROM SILK ROADS TO SMART LUBRICANTS: THE EVOLUTION OF MACHINERY MAINTENANCE IN ASIA
Asia, a continent of resilience and innovation, has evolved remarkably from its ancient Silk Road days to modern industrial hubs.
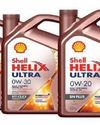
SHELL GROUP SEEKS CCI CLEARANCE FOR RAJ PETRO ACQUISITION
Shell Group, the global energy giant, has approached the Competition Commission of India (CCI) for approval to acquire a 100% stake in Raj Petro Specialities Private Limited.
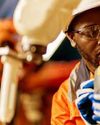
DECODING THE MIX: A GUIDE TO LUBRICANT COMPATIBILITY
Lubricants play a vital role in the intricate world of machinery.
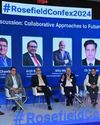
2ND ROSEFIELD CONFERENCE FOR LUBRICANTS AND FUELS: A MILESTONE IN INNOVATION AND COLLABORATION
The 2nd Rosefield Conference for Lubricants and Fuels was a resounding success, attracting over 400 global delegates for two days of insightful discussions and networking.