The application of double wall jacketed pipeline in sulfur recovery units of refinery plays a major role in productivity of sulfur. The sulfur content in crude oil may contain 0.22 wt% as obtained by detailed assay report. This sulfur has been extracted from various hydrocarbon processing units as sour water. Further the sour water processed in sulfur recovery unit to produce sulfur in solid powder form. The molten sulfur condenses via sulfur condensers to produce solid sulfur. The molten sulfur transferred to double wall jacketed pipeline and its failure case study is discussed. An improper design results in internal and external corrosion of internal core pipe deteriorate the pipe within five years. Root cause is analyzed and possible ways to mitigate similar failures is suggested.
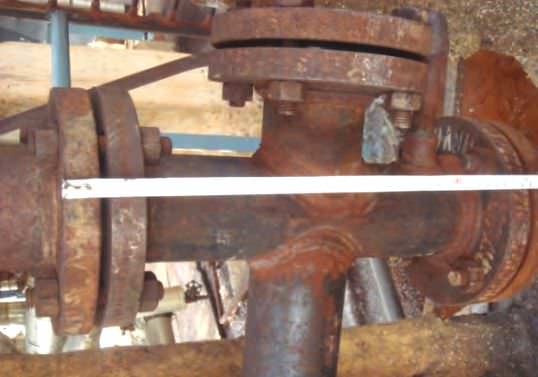
The double wall pipeline is utilized in petroleum refineries and chemical process industries for maintaining liquid sulfur in melting temperature or not below sulfur condense temperature within internal pipe or similar fluid services in similar piping. The low pressure steam supplied within external pipe transfers heat to internal pipe through its wall thickness. Heat transfer depend wall thickness, corrosion scale deposit on inner and outer surfaces of internal pipe, steam temperature, sulfur temperature and material of pipe. One such jacketed pipeline was failed during service is discussed in this short technical paper. The inner pipe contains molten liquid sulfur and outer pipe contains low pressure steam. The nominal pipe size of inner pipe and outer pipe is 50 mm and 75 mm respectively. Both the pipes were made up of ASTM SA106 Grade B carbon steel with design pressure of 0.9 kg/cm2 and design temperature of 250 deg C. The pipelines were operated at 0.11 kg/cm2 pressure and 160 deg C temperature. Frequent failures were observed on double wall piping system and new pipes were installed. It constitutes major breakdown of units and loss of revenue. The insulation was provided for complete double wall piping network. The failure was confirmed by pressure drop within internal pipe due to molten sulfur clogging resulted in reduction of pipe area for fluid to flow. No external steam leakage was observed. This short review paper discusses the causes, analysis and prevention of failure.
Failure Causes and Analysis
Diese Geschichte stammt aus der August 2018-Ausgabe von Chemical Engineering World.
Starten Sie Ihre 7-tägige kostenlose Testversion von Magzter GOLD, um auf Tausende kuratierte Premium-Storys sowie über 8.000 Zeitschriften und Zeitungen zuzugreifen.
Bereits Abonnent ? Anmelden
Diese Geschichte stammt aus der August 2018-Ausgabe von Chemical Engineering World.
Starten Sie Ihre 7-tägige kostenlose Testversion von Magzter GOLD, um auf Tausende kuratierte Premium-Storys sowie über 8.000 Zeitschriften und Zeitungen zuzugreifen.
Bereits Abonnent? Anmelden
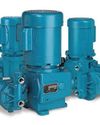
Sizing and Selecting the proper Metering Pump
In process application, large amounts of chemicals are used during daily operations and the volumes of chemicals are large and very precise, with exact amounts delivered according to strict injection schedules. Thus the pressures - from very high to very low – for injecting the chemicals should be governed precisely. Metering pumps have—whether mechanically, hydraulically or electronically actuated—raised to the fore as a technology of first choice for the injection of chemicals in processing and agricultural applications, but within the realm of metering pumps there are many different styles and modes of operation. The article explains the different metering-pump technologies and illustrates how the user should select the proper size and style depending on the injection application for which the pump will be tasked.
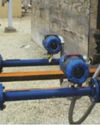
How Two Petrochemical Plants Improved Level And Flow Measurement
How Two Petrochemical Plants Improved Level And Flow Measurement

Just The Right Dose Of Intelligence
Nothing herein shall constitute an offer to sell, or a solicitation of an offer to buy. The ACOPOStrak product is not available for sale into the United States of America until September 2018.
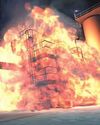
Hunting For Hazards
Leaving no stone unturned, no nook or corner unchecked, till we identify all hazards that threaten our installation or personnel or public
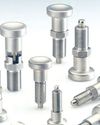
Indexing Plungers For Ultimate Demands In Terms Of Corrosion Resistance, Hygiene And Material Quality
Indexing Plungers For Ultimate Demands In Terms Of Corrosion Resistance, Hygiene And Material Quality
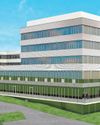
ABB to Invest 100 Million in Global Innovation & Training Campus
ABB makes largest organic investment in industrial automation at home of B&R in Austria One year after announcing its acquisition of B&R (Bernecker + Rainer Industrie-Elektronik GmbH), ABB is to invest €100 million in Austria to build a state-of-the-art innovation and training campus at the home of B&R in Eggelsberg, Upper Austria. It is the largest organic investment in industrial automation in ABB’s more than 130-year history and lays the foundation for around 1,000 new high-tech jobs in Austria.
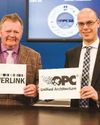
Secure & Seamless Communication With Powerlink & OPC UA
An OPC UA companion specification is now available for POWERLINK according to a joint announcement by the OPC Foundation and the Ethernet POWERLINK Standardization Group (EPSG). The companion specification describes how payload data is exchanged between POWERLINK and any OPC UA platform. The result is integrated communication from the sensor to the cloud – without any interfaces whatsoever.​​​​​​​
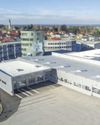
B&R Expands Gilgenberg Site
Automation specialist invests in production, office space and logistics.
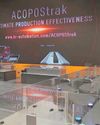
Unmatched Efficiency With High-Speed Diverters
B&R presents flexible transport system at Hannover Messe.
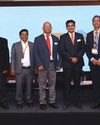
Digitalization Is Not An Option, But A Must
B&R India explores IIoT topics at 4th annual Innovation Day.