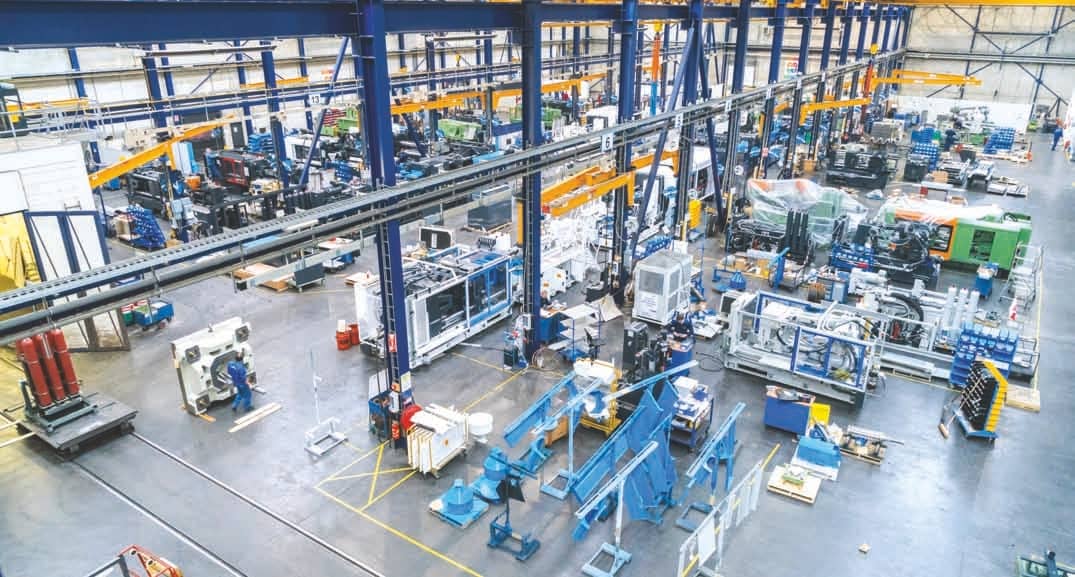
Market demands and recent trends point towards injection moulding solutions moving beyond the traditional requirements. At K 2019, the global plastics industry saw a broad portfolio of injection moulding solutions that can meet specific needs of customers and more.
Stork IMM (Injection Moulding Machines) has supported its customers in the plastics industry since 1968. Over the years, it has developed injection moulding solutions that are adapted to the end product they have to fabricate. At K show, Stork IMM and Brink B.V. joined forces to exhibit under the slogan “Let’s Go Dutch”, which can be interpreted in several ways. In the first instance, “Let’s go Dutch” is the obvious choice for these two Dutch companies, Stork IMM and Brink B.V., as it combined the best of the two companies’ native Dutch heritage and passion for excellence in developing packaging​ solutions for the plastics processing market. “Let’s go Dutch” is also a colloquial term that means to “share the cost” and to Stork IMM, it portrays a clear reflection of the independent nature of these two companies but also their ability to easily co-operate and harness their common history, language, and proximity to each other.
Over the years Stork has specialised in extremely rapid injection moulding machines. The company’s machines are widely applicable and are fully adapted to the end products that would have to be manufactured.
Founded in 1963, the Brink Group has been manufacturing exclusively for the packaging industry high-quality fast-running injection moulds and since 1977 also technology-driven automated systems. With offices and manufacturing centrally located in The Netherlands and joint ventures in South Africa and Russia, Brink sells through a comprehensive channel of customers to more than 70 countries worldwide.
Diese Geschichte stammt aus der December 2019-Ausgabe von International Plastics News for Asia.
Starten Sie Ihre 7-tägige kostenlose Testversion von Magzter GOLD, um auf Tausende kuratierte Premium-Storys sowie über 8.000 Zeitschriften und Zeitungen zuzugreifen.
Bereits Abonnent ? Anmelden
Diese Geschichte stammt aus der December 2019-Ausgabe von International Plastics News for Asia.
Starten Sie Ihre 7-tägige kostenlose Testversion von Magzter GOLD, um auf Tausende kuratierte Premium-Storys sowie über 8.000 Zeitschriften und Zeitungen zuzugreifen.
Bereits Abonnent? Anmelden
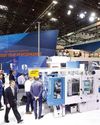
Industry innovations aimed towards a greener future
Sustainability and circular economy, energy saving technologies, high-performance materials with enhanced properties, and cost-efficient production processes are expected to dominate the plastics industry in 2022 and beyond.
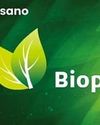
Special extrusion lines for bioplastic compounds
The biodegradable and compostable plastics sector is growing steadily, and this is partly due to the fact that several measures have been taken, especially in the EU, to cut down on single-use plastics.
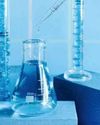
Plastics revolutionise medical device production
The coronavirus pandemic has brought into focus the urgent need for medical supplies – which included medical disposables, medical devices, laboratory equipment, and many others.
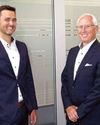
Spinning and recycling go together in a single step
As a medium-sized German machine construction business, BB Engineering has been manufacturing components and systems for synthetic fibre and film production for more than 20 years.
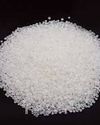
Advanced high-performance light stabilisers
A range of high-performance light stabilisers with enhanced properties are now being made available.
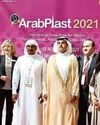
ArabPlast holds successful edition
The 15th Edition of ArabPlast was held on 15-18November 2021 at the Dubai World Trade Centre, Dubai, U.A.E. Spanning over 28 years, ArabPlast is an exclusive event for plastics, petrochemicals, packaging and rubber industry, and serves as an attractive platform where global industry players show off their products to the Middle East market.
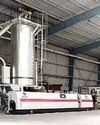
Food-grade plastics recycling facility installed in India
The well-established Indian recycler commissioned a PET bottle-to-bottle and a post-consumer polyolefin recycling line from Starlinger in mid-September.
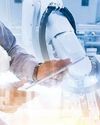
How to bring down downtime in manufacturing
For most of us, the word downtime conjures images of relaxation.
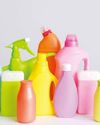
Optimistic forecast for blow moulded plastics market
Growing demand from key applications is a key factor in the projected growth of the blow moulding sector.
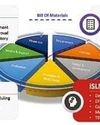
The benefits of dedicated system for mould development
When it comes to useful tools that can enhance teamwork efficiency, we usually think of the Product Lifecycle Management (PLM) systems.