The value of CNC (computer numerical controlled) technology is a given among most production shops—even if they don't have one.
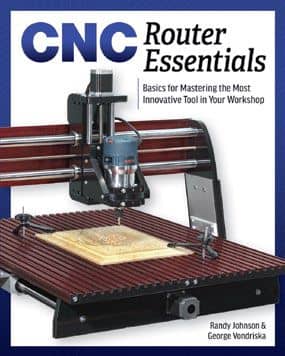
But small shops and hobby woodworkers, CNC is often quickly dismissed as not needed or wanted. The reasons include cost, the potential learning curve, an unclear need, and a concern that “it's not real woodworking.” As CNC routers continue to decrease in price and increasing in availability at woodworking retailers, there is more and more access to information, classes, and community feedback on how to utilize this valuable tool. And, while it’s true that a CNC router can automate the operations of many other machines (i.e. table saw, bandsaw, drill, router), that’s not necessarily a bad thing.
The versatility of the CNC is perhaps the best justification for adding it to a small shop. What other tool has the ability to cut complex and odd shaped pieces with such ease? Curved furniture parts, templates, jigs, and rough carvings are all handled easily with CNC. It’s also a great companion tool for prototyping, because it allows a woodworker to quickly create multiple versions of a design or a sample for a client. It takes the tedium out of many operations and allows the woodworker to focus on other, more creative aspects, such as design and craftsmanship.
The more one eliminates his or her preconceived notions and works with a CNC router, the more one discovers the many interesting and useful ways that it can be used in the shop and on projects. So rather than seeing a CNC router as an unnecessary and expensive gadget or a threat to the essence of woodworking, it can be more helpful to view it as a useful tool that can augment your hard-earned skills, while offering versatility like no other.
MACHINE MECHANICS
Diese Geschichte stammt aus der November-December 2018-Ausgabe von Woodworker West.
Starten Sie Ihre 7-tägige kostenlose Testversion von Magzter GOLD, um auf Tausende kuratierte Premium-Storys sowie über 8.000 Zeitschriften und Zeitungen zuzugreifen.
Bereits Abonnent ? Anmelden
Diese Geschichte stammt aus der November-December 2018-Ausgabe von Woodworker West.
Starten Sie Ihre 7-tägige kostenlose Testversion von Magzter GOLD, um auf Tausende kuratierte Premium-Storys sowie über 8.000 Zeitschriften und Zeitungen zuzugreifen.
Bereits Abonnent? Anmelden
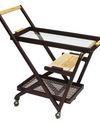
Education: 2022 Design Emphasis
The next generation of furniture designers were on display at the 2022 Design Emphasis, the biennial student design competition exhibition held in conjunction with last summer’s International Woodworking Fair IWF) in Atlanta, GA.
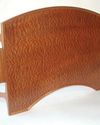
Profile: Leo Litto
Leo Litto of Austin, TX is an award-winning maker of heirloom quality furniture. Here is Leo's story, in his own words:
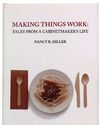
Tools & Techniques
It’s All Problems
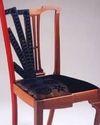
Profile: John P. McCormack
As the Port Townsend School of Woodworking welcomes master woodworkers from around the Northwest to their November Woodworking Show, we caught up with its newest faculty member, John P. McCormack. Here is John’s story in his own words:
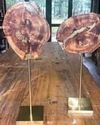
From David Marks Studio- Patina Applications & Questions
For years, many of you have read my discussions about gilding and chemical patination techniques, but are unsure about its application to your own work. I'd like to share a recent email from Sandra Walkin of Louisiana, who took my Gilding & Chemical & Patination class and a 2-day private class in 2015:
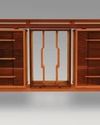
Education: NW Woodworking Studio
Education: NW Woodworking Studio
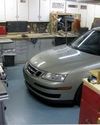
Tools & Techniques Small Shop Design
Tools & Techniques Small Shop Design
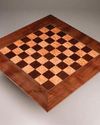
From David Marks Studio Answering Reader's Questions
From David Marks Studio Answering Reader's Questions
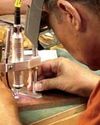
Profile: Marco Cecala
Marco Cecala of Phoenix, AZ is a talented craftsman, beginning a transition into full-time furnituremaking. Here is Marco’s story, in his own words:
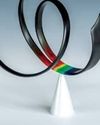
Turning Topics AAW Members' Exhibition
Continuum