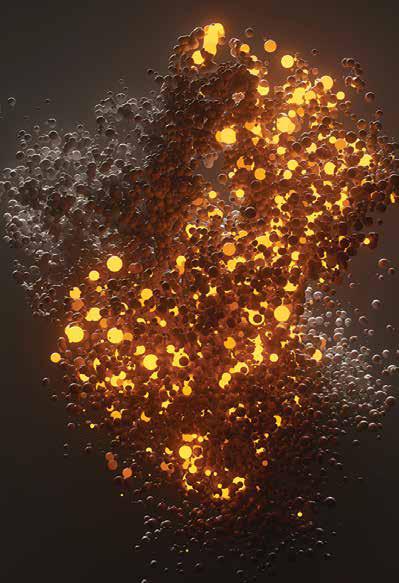
Factor: A2P
If you have been in the Maintenance/ Reliability space for any length of time, you may have heard someone "We need to drain or change the oil because of the number of particles that can be seen." While checking for contaminants is a must for any great inspection program, it is important to know that the particles doing the most damage to machine parts are far too small to be seen with the naked eye.
Why Small Particles Matter
More Without a magnifying glass or microscope, the human eye can only see particles down to about 40 microns in size. The particles doing the most damage to our lubricants are in the 3-10 micron range, way smaller than what can be seen on a typical visual inspection of the lubricant. These particles are more concerning than their larger counterparts because they are close to the size of typical film thicknesses, which can allow them to go through the load zone, causing damage to machine parts.
- Hydrodynamic Lubrication (Sliding) Typical oil films are 5-20 microns.
- Elastohydrodynamic Lubrication (Rolling) Oil films can be less than 1 micron.
Breaking it Down
Diese Geschichte stammt aus der January - February 2023-Ausgabe von MACHINERY LUBRICATION INDIA.
Starten Sie Ihre 7-tägige kostenlose Testversion von Magzter GOLD, um auf Tausende kuratierte Premium-Storys sowie über 8.000 Zeitschriften und Zeitungen zuzugreifen.
Bereits Abonnent ? Anmelden
Diese Geschichte stammt aus der January - February 2023-Ausgabe von MACHINERY LUBRICATION INDIA.
Starten Sie Ihre 7-tägige kostenlose Testversion von Magzter GOLD, um auf Tausende kuratierte Premium-Storys sowie über 8.000 Zeitschriften und Zeitungen zuzugreifen.
Bereits Abonnent? Anmelden
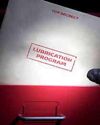
The Secrets For Implementing A Clean lubricant Program
If you could find an investment that guaranteed a return 40 times greater than your initial investment, you probably wouldn't pass it up.
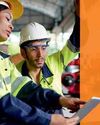
MAINTAIN? REPAIR? REPLACE?
When considering the life of any asset, the question arises: what types of interventions should be planned to keep it operating or to restore operation in the event of its failure?
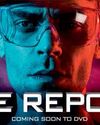
Engineering Reports Should Be Like Bad Movies
I'm frequently asked to review engineering reports, and I'm continually baffled by how many engineers want to take their readers on a journey instead of getting to the point.
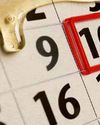
WHY SCHEDULED OIL CHANGES AREN'T ENOUGH TO MITIGATE LUBRICANT CONTAMINATION
There are few problems more insidious or damaging to large industrial machinery than contaminated lubricant.
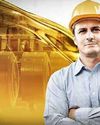
LUBRICATION CONTAMINATION PREVENTION
How many articles have you read, or seminars listened to, that tout the value of contamination control? If you are like me, they number in the hundreds—if not thousands. One thing about these articles and seminars that bothers me is the word “control”.
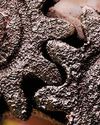
LUBRICANT CONTAMINATION PREVENTION AND MITIGATION: A Guide For Maintenance Professionals
Lubricants are essential for the smooth and efficient operation of many types of machinery, from engines and turbines to gears and bearings.
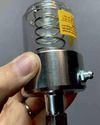
TASK-BASED TRAINING | INSPECTING A SINGLE-POINT LUBRICATOR
A single-point lubricator is a device engineered to attach to a single unit to regularly and automatically deliver a small amount of clean grease or lubricating oil to a specific area.
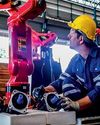
TOP LEADERSHIP FOCUSES FOR IMPROVED RELIABILITY AND COST REDUCTION
Here’s a scenario that may sound eerily familiar – you have a new reliability initiative.
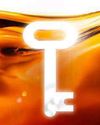
4 KEY ELEMENTS FOR INTERPRETING AN OIL ANALYSIS REPORT
Years ago, a customer came into my office, visibly upset. He had just received his second oil analysis report for one of his Caterpillar gas engines.
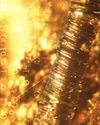
ASTM ENHANCEMENTS TO MICROSCOPIC PARTICLE IDENTIFICATION AND DOCUMENTATION
In 1982, Daniel Anderson published his influential book, \"Wear Particle Atlas\", which describes, sizes, and classifies particles found in oil.