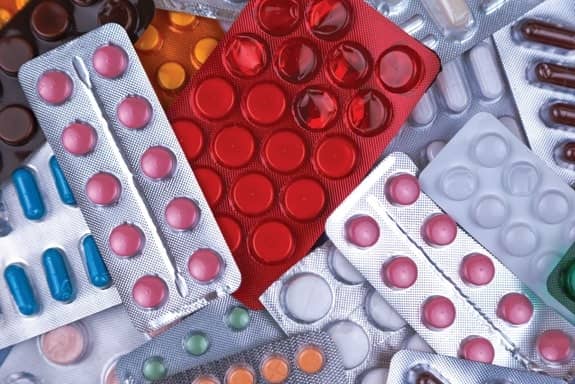
The pharmaceuticals industry is at the core of the manufacturing capabilities of any country and this importance has been brought to the forefront in an unprecedented manner. With the pandemic calling upon all industries to bring into action their very best innovation and resourcefulness skills, there is no doubt that the one sector which has been in the spotlight is the pharma and ancillary industries. This pressure to develop a vaccine and much needed other medicines also came with an impetus to the pharma packaging industry to keep pace, and in many cases, evolve at a greater speed –to get the medicines to the end-user in a safe, hygienic and efficient manner. There is no doubt that the past year has seen considerable use of technological concepts in pharma packaging solutions.
Innovations at its Best
The Marchesini Group, an Italian based company, has introduced the ultra-technological blister line which includes the Integra 520 V and the fast bundler FA 04. Boasting of delivering 520 blisters and 500 cartons per minute, the line can pack blisters into cartons and bundle them at high speed. The Integra 520 V integrates two machines — a thermoformer and a cartoner and is the fastest robotised integrated blister line ever created by the firm.
Equipped with features of its previous model — the Integra 320, the new line also comes with new pushers, a drum-type carton opener to deal with high speeds and a leaflet pick-and-place system. The blister line can be used for single-blister cartons and the blisters are inserted into the cartons by an ingenious product insertion unit, the MA 500. The company states that the MA 500 is designed to handle all kinds of carton closure: tuck-in or glued flap and various other combinations. The new fast bundler FA 04 can handle a production flow of 500 cartons per minute, arranged in 50 bundles of ten cartons.
Small Footprint
この記事は ET Polymers の June - July 2021 版に掲載されています。
7 日間の Magzter GOLD 無料トライアルを開始して、何千もの厳選されたプレミアム ストーリー、9,000 以上の雑誌や新聞にアクセスしてください。
すでに購読者です ? サインイン
この記事は ET Polymers の June - July 2021 版に掲載されています。
7 日間の Magzter GOLD 無料トライアルを開始して、何千もの厳選されたプレミアム ストーリー、9,000 以上の雑誌や新聞にアクセスしてください。
すでに購読者です? サインイン
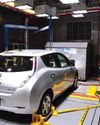
The Changing Face Of Mobility
A brief look at the salient points on how plastics is transforming automotive manufacturing
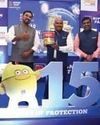
Nippon Launches Weatherbond PRO
Nippon Paint (India) Private Limited (Decorative Division) Asia’s leading paint manufacturer launched the advertising campaign for Weatherbond PRO – the high durable exterior emulsion offering up to 15 years of protection against extreme climate conditions like prolonged exposure to heat, and heavy spells of rain. Based on extensive research done by Nippon Paint’s R&D team, this product was developed for customers who need advance protection for their home exteriors in terms of extended fresh look, strong waterproofing and protection from Algal and Fungal attacks.
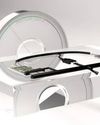
Low-Pressure Molding Adopted Across Industries
Henkel’s Technomelt Low-Pressure Molding technology meets demands for encapsulation of electronics and medical components
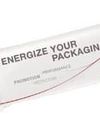
TotalEnergies and Jindal Films To introduce Certified Circular Polypropylene
TotalEnergies and Jindal Films have joined forces to produce more sustainable flexible food packaging and labels. Using advanced recycling technology from Plastic Energy, TotalEnergies will supply Jindal Films with Certified Circular Polypropylene produced from postconsumer plastic waste. This new value-chain collaboration will divert plastic waste currently destined for incineration and landfill because it is too complex to recycle through existing schemes.
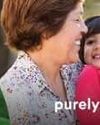
Lenzing's VEOCEL™ Brand Launches Hydrophobic Lyocell Fibres With Dry Technology
In its quest to drive greater sustainability in the personal care and hygiene industry, the VEOCEL™ brand has launched a new offering: VEOCEL™ branded lyocell fibres with dry technology which are naturally smooth and gentle on skin, ensuring comfort for sensitive skin. Absorbent hygiene products are an indispensable part of many consumers’ lives and are relied upon daily. As these are essential items, it is important that they should offer maximum comfort and relief to the user. This is demonstrated by the new VEOCEL™ branded lyocell fibres which have the capacity to provide a high level of comfort, softness and dryness, when applied in these types of products.
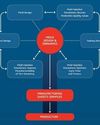
Simulating Injection Molding for Efficiency
Producing high-quality, plastic injection-moulded parts more quickly and cost-effectively has become a critical factor for manufacturing success in today’s global market. Instead of engaging in slow, expensive prototype iterations and test cycles to satisfy manufacturing requirements, designers, mold makers, and manufacturing professionals can leverage SOLIDWORKS® Plastics mold-filling simulation software to optimise parts for manufacturability, refine tooling to improve quality and shorten cycle times to reduce manufacturing costs
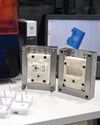
Leveraging 3D Printing for optimised Injection Molds
A guideline from Formlabs on the factors to consider before using stereolithography (SLA) 3D printed molds in the injection molding process to lower costs, reduce lead times, and bring better products to market
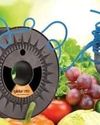
iglidur I151 for FDA-compliant, Detectable, Wear Resistant Parts In Food Technology
igus has developed a blue, food-compatible tribo-filament for cost effective 3D printing of special parts. iglidur I151 is blue, prints easily, and has an optimal coefficient of friction and wear. The new tribo-filament is a refinement of the easy-to-machine igus iglidur I150 all-rounder filament. Because it is blue, it can be used to manufacture special parts that are optically detectable in the food industry. Food compatibility according to the FDA and to EU Regulation 10/2011 also qualifies the high-performance polymer for use in the food and cosmetics industries.
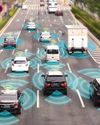
Exceptional Warpage Control
SABIC’s new LNP™ THERMOCOMP™ compounds deliver exceptional warpage control
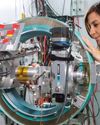
Digital Transformation in Plastics
Automation in the plastics industry is becoming more complex, the pace of innovation is accelerating, and competitive pressure is increasing. Open and safe automation makes it possible to combine traditional mechanical engineering with the latest Industry 4.0 technologies – Lets take a look at how Industry 4.0 is transforming the plastics sector