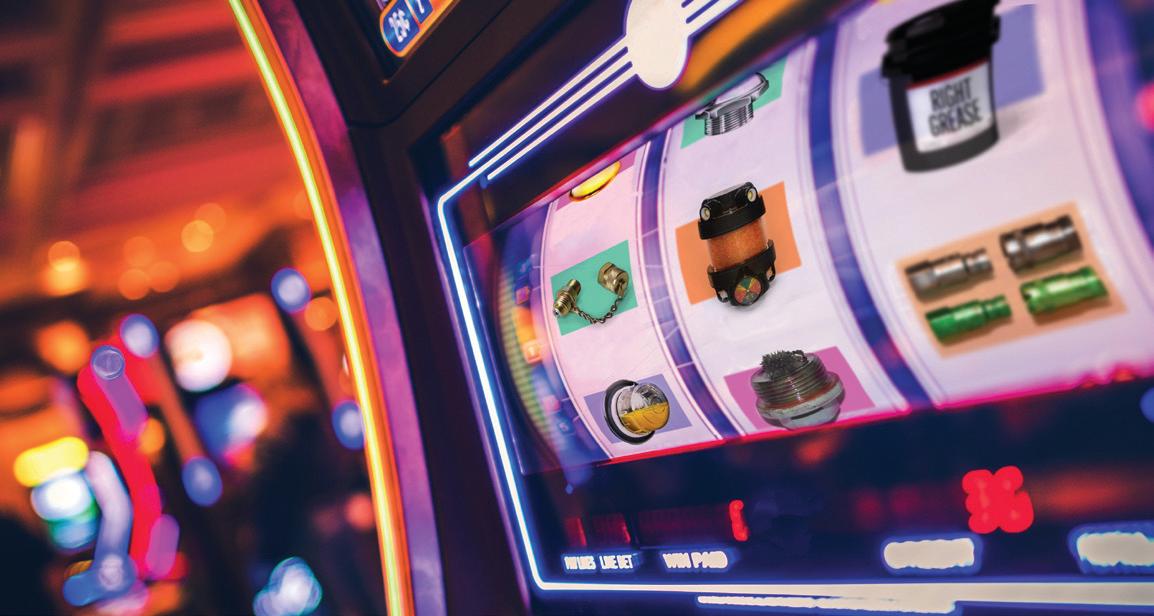
The landscape of manufacturing and industrial processes is constantly changing. Historically, titans of industry capitalized on large, cumbersome, overbuilt, sluggish equipment that had to be continuously maintained by a labor force that was paid an incredibly low wage. Modern industry is stressed to operate in a leaner landscape with fewer workers, purpose-built equipment and margins that, in many cases, are razor thin. This leads to improvement activities that get more and more out of less and less: more product and profit out of fewer people and with fewer failures or disruptions to business. In order to do this, practices and equipment both have to evolve to maintain pace with demands.
Fewer items are more scrutinized than the facility's physical assets; we have to make sure they perform how they are supposed to, when they are supposed to, and for however long they are supposed to. For this to happen, many factors have to be balanced, and often the equipment may not be capable of performing to this level in its current state. A higher state of configuration must be achieved — an optimum state that allows maintenance, operations and reliability to perform all necessary checks on the equipment without interrupting its service, all while maintaining or improving the inherent reliability of the piece of equipment.
Changing the configuration of assets or modifying them to improve performance is not a task that should be taken on lightly. To best modify the equipment for performance, we would first have to define how we want the equipment to improve. You can define optimized performance in many areas, and depending on your organizational goals, the changes to the equipment would have to follow suit. What follows are some of the most common reasons for modifying equipment to increase performance.
この記事は MACHINERY LUBRICATION INDIA の May- June 2023 版に掲載されています。
7 日間の Magzter GOLD 無料トライアルを開始して、何千もの厳選されたプレミアム ストーリー、9,000 以上の雑誌や新聞にアクセスしてください。
すでに購読者です ? サインイン
この記事は MACHINERY LUBRICATION INDIA の May- June 2023 版に掲載されています。
7 日間の Magzter GOLD 無料トライアルを開始して、何千もの厳選されたプレミアム ストーリー、9,000 以上の雑誌や新聞にアクセスしてください。
すでに購読者です? サインイン
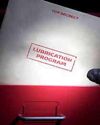
The Secrets For Implementing A Clean lubricant Program
If you could find an investment that guaranteed a return 40 times greater than your initial investment, you probably wouldn't pass it up.
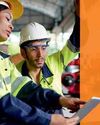
MAINTAIN? REPAIR? REPLACE?
When considering the life of any asset, the question arises: what types of interventions should be planned to keep it operating or to restore operation in the event of its failure?
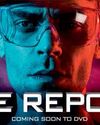
Engineering Reports Should Be Like Bad Movies
I'm frequently asked to review engineering reports, and I'm continually baffled by how many engineers want to take their readers on a journey instead of getting to the point.
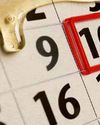
WHY SCHEDULED OIL CHANGES AREN'T ENOUGH TO MITIGATE LUBRICANT CONTAMINATION
There are few problems more insidious or damaging to large industrial machinery than contaminated lubricant.
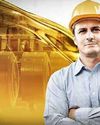
LUBRICATION CONTAMINATION PREVENTION
How many articles have you read, or seminars listened to, that tout the value of contamination control? If you are like me, they number in the hundreds—if not thousands. One thing about these articles and seminars that bothers me is the word “control”.
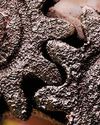
LUBRICANT CONTAMINATION PREVENTION AND MITIGATION: A Guide For Maintenance Professionals
Lubricants are essential for the smooth and efficient operation of many types of machinery, from engines and turbines to gears and bearings.
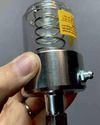
TASK-BASED TRAINING | INSPECTING A SINGLE-POINT LUBRICATOR
A single-point lubricator is a device engineered to attach to a single unit to regularly and automatically deliver a small amount of clean grease or lubricating oil to a specific area.
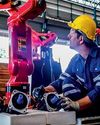
TOP LEADERSHIP FOCUSES FOR IMPROVED RELIABILITY AND COST REDUCTION
Here’s a scenario that may sound eerily familiar – you have a new reliability initiative.
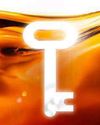
4 KEY ELEMENTS FOR INTERPRETING AN OIL ANALYSIS REPORT
Years ago, a customer came into my office, visibly upset. He had just received his second oil analysis report for one of his Caterpillar gas engines.
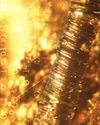
ASTM ENHANCEMENTS TO MICROSCOPIC PARTICLE IDENTIFICATION AND DOCUMENTATION
In 1982, Daniel Anderson published his influential book, \"Wear Particle Atlas\", which describes, sizes, and classifies particles found in oil.