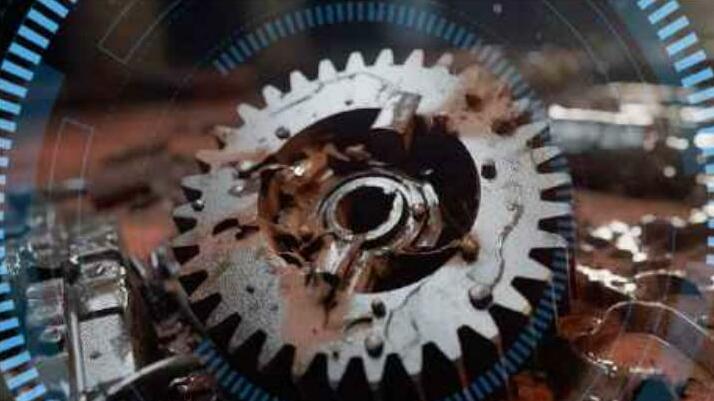
Root cause analysis (RCA) is defined as a systematic process for identifying the root causes of problems or events and an action plan for responding to them. Many organizations tend to focus on or single out one factor when trying to identify a cause, which leads to an incomplete resolution.
Root cause analysis helps avoid this tendency and looks at the event as a whole. Another common occurrence is for companies to treat the symptoms rather than the actual underlying problems contributing to the issue, leading to recurrence.
Using root cause analysis to analyze problems or events should help you tackle the primary goal of determining:
- What happened
- How it happened
- Why it happened
- Actions for preventing recurrence of the issues
In the end, root cause analysis boils down to three goals. The first goal is just as the name implies: to discover the root cause of a problem or event. The second goal is to understand how to fix, compensate for or learn from issues derived from the root cause. The third and most important goal is to apply what you learn from the analysis to prevent issues in the future.
How to Conduct a Root Cause Analysis (RCA)
Root cause analysis can be used in a variety of settings across multiple industries. Each industry might conduct the analysis in a slightly different way, but most follow the same general five-step process when investigating issues involving heavy machinery. This process was laid out by the United States Department of Energy (DOE-NESTD-1004-92) back in 1992. Root cause analysis is commonly referred to as detective work at its finest. You'll see similarities between how a detective works to solve a case and how manufacturers can figure out the root cause of an issue in the five-step process.
Phase 1 - Data Collection
ãã®èšäºã¯ MACHINERY LUBRICATION INDIA ã® January - February 2024 çã«æ²èŒãããŠããŸãã
7 æ¥éã® Magzter GOLD ç¡æãã©ã€ã¢ã«ãéå§ããŠãäœåãã®å³éžããããã¬ãã¢ã ã¹ããŒãªãŒã9,000 以äžã®éèªãæ°èã«ã¢ã¯ã»ã¹ããŠãã ããã
ãã§ã«è³Œèªè ã§ã ?  ãµã€ã³ã€ã³
ãã®èšäºã¯ MACHINERY LUBRICATION INDIA ã® January - February 2024 çã«æ²èŒãããŠããŸãã
7 æ¥éã® Magzter GOLD ç¡æãã©ã€ã¢ã«ãéå§ããŠãäœåãã®å³éžããããã¬ãã¢ã ã¹ããŒãªãŒã9,000 以äžã®éèªãæ°èã«ã¢ã¯ã»ã¹ããŠãã ããã
ãã§ã«è³Œèªè ã§ã? ãµã€ã³ã€ã³
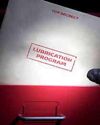
The Secrets For Implementing A Clean lubricant Program
If you could find an investment that guaranteed a return 40 times greater than your initial investment, you probably wouldn't pass it up.
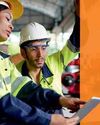
MAINTAIN? REPAIR? REPLACE?
When considering the life of any asset, the question arises: what types of interventions should be planned to keep it operating or to restore operation in the event of its failure?
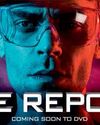
Engineering Reports Should Be Like Bad Movies
I'm frequently asked to review engineering reports, and I'm continually baffled by how many engineers want to take their readers on a journey instead of getting to the point.
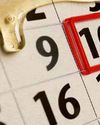
WHY SCHEDULED OIL CHANGES AREN'T ENOUGH TO MITIGATE LUBRICANT CONTAMINATION
There are few problems more insidious or damaging to large industrial machinery than contaminated lubricant.
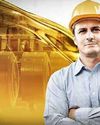
LUBRICATION CONTAMINATION PREVENTION
How many articles have you read, or seminars listened to, that tout the value of contamination control? If you are like me, they number in the hundredsâif not thousands. One thing about these articles and seminars that bothers me is the word âcontrolâ.
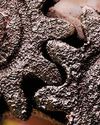
LUBRICANT CONTAMINATION PREVENTION AND MITIGATION: A Guide For Maintenance Professionals
Lubricants are essential for the smooth and efficient operation of many types of machinery, from engines and turbines to gears and bearings.
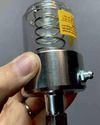
TASK-BASED TRAINING | INSPECTING A SINGLE-POINT LUBRICATOR
A single-point lubricator is a device engineered to attach to a single unit to regularly and automatically deliver a small amount of clean grease or lubricating oil to a specific area.
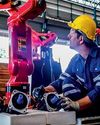
TOP LEADERSHIP FOCUSES FOR IMPROVED RELIABILITY AND COST REDUCTION
Hereâs a scenario that may sound eerily familiar â you have a new reliability initiative.
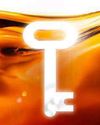
4 KEY ELEMENTS FOR INTERPRETING AN OIL ANALYSIS REPORT
Years ago, a customer came into my office, visibly upset. He had just received his second oil analysis report for one of his Caterpillar gas engines.
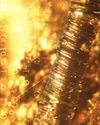
ASTM ENHANCEMENTS TO MICROSCOPIC PARTICLE IDENTIFICATION AND DOCUMENTATION
In 1982, Daniel Anderson published his influential book, \"Wear Particle Atlas\", which describes, sizes, and classifies particles found in oil.