A Company Specialising in Design, Development and Manufacturing of Plastic Injection Moulds for Various Industries Used Simulation Software to Decrease the Construction Time and the Number of Potential Failures.
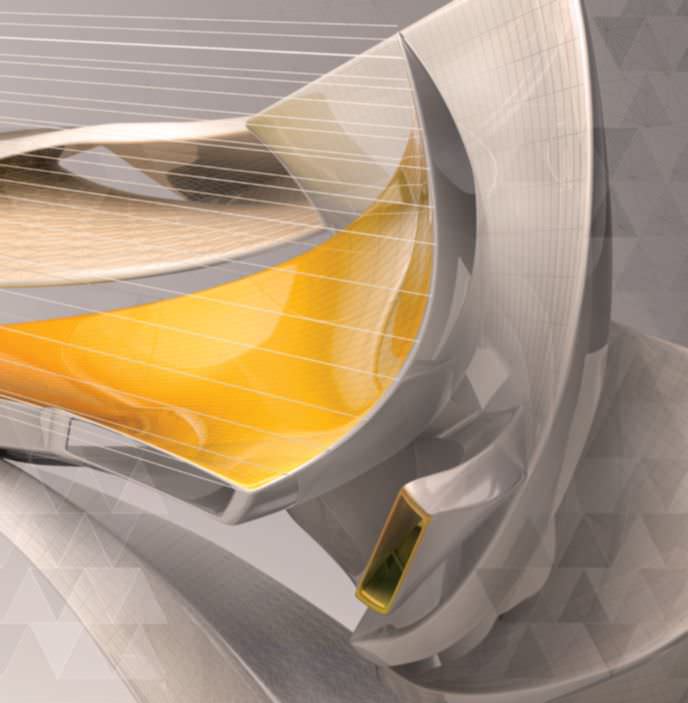
Sridevi Tool Engineers specialises in design, development and manufacturing of plastic injection moulds for automobile, white goods, luggage and various other engineering industries.
Established in 1972, it is one of the largest commercial tool rooms in India having more than 40 years of experience in producing tools for both domestic and foreign markets. The company majorly produce moulds for automotive trims, consoles, pillars, headlamp housings, air filters, exhaust assemblies, instrument panel and its child parts, grills, motorcycle fenders etc.
Sridevi Tool Engineers has fully equipped state of the art tool room and project management skills make them one of the most preferred tooling suppliers to OEMs.
The Challenge
Nowadays, more and more polymer based products are utilised in the automotive industry, in the medical science and in many other areas. As a result of the continuous developments, novel polymer materials and special processes are developed to accomplish the strict engineering claims.
The competition in the market and the strict requirements for the plastic parts require faster and more accurate mold making. The quality of injection molded thermoplastic parts largely depends on the process parameters. “In the mold development and in the failure analysis the simulation has a great role. Simulation software allows fulfilling the injection molding process in a virtual reality, which helps the mold optimisation, the material and process parameter determination before machining the injection mold. This way decreases the construction time and the number of potential failures,” said Rajendra Rindhe, Assistant Manager CAE
Denne historien er fra Aug - Sept 2017-utgaven av ET Polymers.
Start din 7-dagers gratis prøveperiode på Magzter GOLD for å få tilgang til tusenvis av utvalgte premiumhistorier og 9000+ magasiner og aviser.
Allerede abonnent ? Logg på
Denne historien er fra Aug - Sept 2017-utgaven av ET Polymers.
Start din 7-dagers gratis prøveperiode på Magzter GOLD for å få tilgang til tusenvis av utvalgte premiumhistorier og 9000+ magasiner og aviser.
Allerede abonnent? Logg på
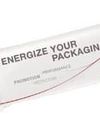
TotalEnergies and Jindal Films To introduce Certified Circular Polypropylene
TotalEnergies and Jindal Films have joined forces to produce more sustainable flexible food packaging and labels. Using advanced recycling technology from Plastic Energy, TotalEnergies will supply Jindal Films with Certified Circular Polypropylene produced from postconsumer plastic waste. This new value-chain collaboration will divert plastic waste currently destined for incineration and landfill because it is too complex to recycle through existing schemes.
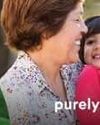
Lenzing's VEOCEL™ Brand Launches Hydrophobic Lyocell Fibres With Dry Technology
In its quest to drive greater sustainability in the personal care and hygiene industry, the VEOCEL™ brand has launched a new offering: VEOCEL™ branded lyocell fibres with dry technology which are naturally smooth and gentle on skin, ensuring comfort for sensitive skin. Absorbent hygiene products are an indispensable part of many consumers’ lives and are relied upon daily. As these are essential items, it is important that they should offer maximum comfort and relief to the user. This is demonstrated by the new VEOCEL™ branded lyocell fibres which have the capacity to provide a high level of comfort, softness and dryness, when applied in these types of products.
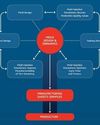
Simulating Injection Molding for Efficiency
Producing high-quality, plastic injection-moulded parts more quickly and cost-effectively has become a critical factor for manufacturing success in today’s global market. Instead of engaging in slow, expensive prototype iterations and test cycles to satisfy manufacturing requirements, designers, mold makers, and manufacturing professionals can leverage SOLIDWORKS® Plastics mold-filling simulation software to optimise parts for manufacturability, refine tooling to improve quality and shorten cycle times to reduce manufacturing costs

Perfecting your Purging Procedures
Determining the source of streaking or contamination in your molded parts is a critical step in perfecting your purging procedures, ultimately saving you time and money. We take a closer look at the nitty-gritty details of purging.
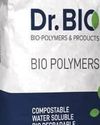
Going Sustainable With Polymers
Hi-Tech International is the first company in the country to manufacture a plantbased bio-polymer – Dr Bio – which can be used to replace single-use and multi-use plastic products with bio-compostable plastic. The Machinist take a closer look…
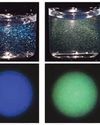
Inspired by Nature
A project researching the effects of structural colouration in nature and translating the same for pigmentation in industrial applications
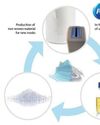
Face (mask) Off: Recycle & Reuse
Fraunhofer, SABIC, and Procter & Gamble join forces in a closed-loop recycling pilot project for single-use facemasks
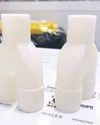
ELIX Polymers Joins The Fight Against Covid-19
Leading ABS producer ELIX Polymers is collaborating with a large group of companies within ClusterMAV, the Advanced Materials Cluster of Catalonia, Spain, in the fight against COVID-19.
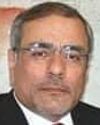
Investing in the Future
Umesh Anand, Managing Director, HPL Additives Limited talks to us about his company and its focus on innovation and sustainability
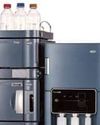
Waters Peptide Multi-Attribute Method for BioAccord System Boosts Innovator and Biosimilar Drug Development
Waters Corporation today introduced a new peptide multi-attribute method (MAM) workflow for the Waters™ BioAccord™ LC-MS System, enabling drug development, manufacturing, and QC scientists to monitor efficacy and safety through the analysis of critical quality attributes (CQAs) of monoclonal antibodies (mAbs) and other protein-based drugs.