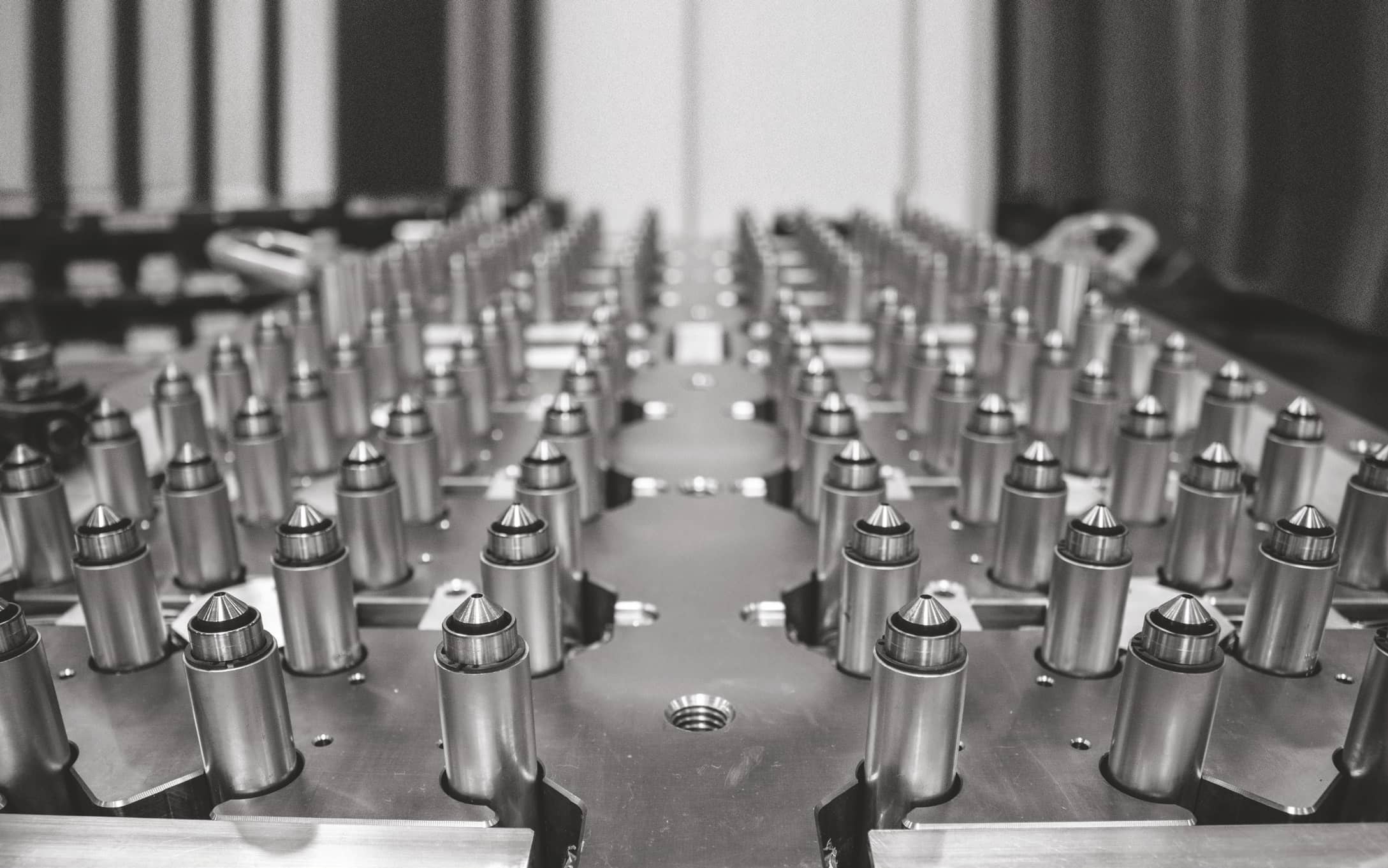
COCA-COLA USES A SPECIFIC SHADE OF red, while one particular shade of blue is what identifies Pepsi.
In consumer packing, as brands keep adding new varieties, demand shorter production runs and develop new designs with increasing frequency, there is increased focus on changing colour at processing. Optimising the injection moulding colour change process to get an accurate colour is the need of the day.
“A poor colour change process can result in extra wasted material, greater downtime, and increased scrap. These can accumulate to higher production costs,” said Derrick Hennebicque, Product Manager, Hot Runners at Husky.
He was making a presentation at a knowledge session webinar on ‘An in-depth look at colour change performance’ presented by Husky and powered by Manufacturing Today. In an engaging delivery, he sought from the audience “an appreciation not only for the importance of colour change but also for all the consideration needed to make it happen; such as design principle, application influences and the importance of colour sequencing.”
REAL-LIFE GAINS
A 32 drop polypropylene closure mould changing from Amber to Natural was reported to need 9000 cycles in 28 hours for the colour change until an approved part of an acceptable colour was produced. With adjustments and solutions from Husky, this was reduced to 215 cycles in 40 minutes. This saved 656 hours of machine time and 10,300 kg of scrap material per year.
With case studies from real life such as these dotting his presentation, Hennebicque demonstrated the value of a high-performance colour change process that businesses and professionals interested in injection moulding would find compelling.
PRINCIPLES AND CONCEPTS
Denne historien er fra April 2022-utgaven av Manufacturing Today.
Start din 7-dagers gratis prøveperiode på Magzter GOLD for å få tilgang til tusenvis av utvalgte premiumhistorier og 9000+ magasiner og aviser.
Allerede abonnent ? Logg på
Denne historien er fra April 2022-utgaven av Manufacturing Today.
Start din 7-dagers gratis prøveperiode på Magzter GOLD for å få tilgang til tusenvis av utvalgte premiumhistorier og 9000+ magasiner og aviser.
Allerede abonnent? Logg på
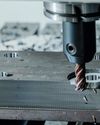
Optimising milling operations
Exploring innovative strategies that are reshaping the milling landscape to meet the challenges of a competitive global market.
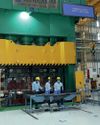
The path to excellence
Tata AutoComp’s Double Deming triumph is testament to quality and innovation
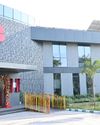
Boosting India's energy efficiency with advanced low voltage motors
Stefan Floeck, Division President of IEC Low Voltage Motors at ABB Motion, discusses the role of low voltage motors in India’s industrial future.
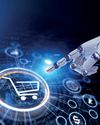
The Tech of E-commerce
Technology is revolutionising e-commerce by enhancing demand forecasting, inventory management, and customer experiences through AI, blockchain, IoT, and real-time data analytics.
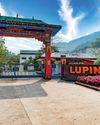
Driving Sustainability and Innovation
A conversation with Rajendra B Chunodkar, President Manufacturing Operations, Lupin
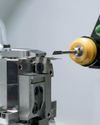
The evolution of machining technologies
The evolution of machining technologies is reshaping the manufacturing landscape, offering unprecedented opportunities for efficiency, precision, and sustainability.
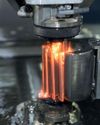
Transforming the future of manufacturing technology
A pre-event report on IMTEX 2025: The premier manufacturing and metal cutting technologies event for
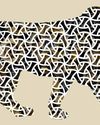
THE MAKE IN INDIA JOURNEY
An analysis of the initiative's impact on the manufacturing sector.
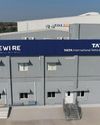
Tata Motors Re.Wi.Re: Innovation meets responsibility
Tata Motors advances circular economy via Re.Wi.Re scrapping facility.
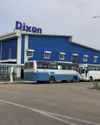
After Apple, Google Pixel set to be manufactured in India
Dixon Technologies' alliance with Compal Electronics is poised to further accelerate India's push to become a global hub for smartphone manufacturing.