Consumer Goods Giant Unilever Iterates 50 Percent Faster With 3d Printing
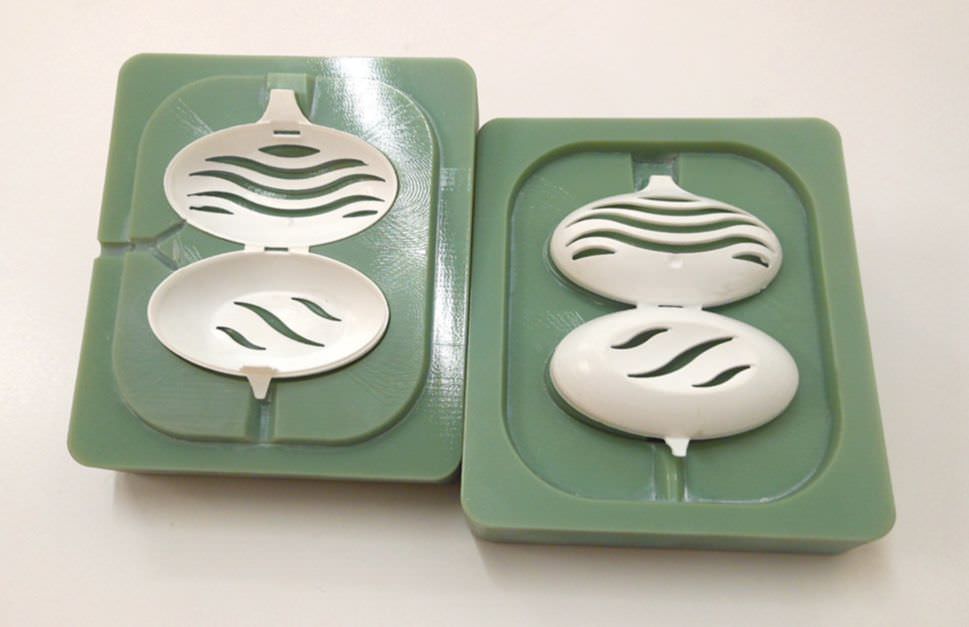
Today’s global market has created a variety of challenges for consumer brands. Products that used to be visibly unchanged for years may now be in a state of continuous evolution. The on-going development of product design can be time-consuming and costly for companies because of the scale and processes involved. This is why the Italian division of international consumer goods giant, Unilever, invested in 3D printing to make injection moulds, blow moulds and thermoform (vacuum) moulds for accelerated prototype and part development without the need for conventional tooling.
Competitive time and cost Challenge With more than 400 brands in its four divisions, Unilever needs to ensure that all are competitive, meet ever-changing product standards and differentiate themselves on the shelf. Developing and refining components for the Home Care, Personal Care, Food and Refreshment divisions is, in part, the responsibility of Unilever’s facility in Caselpusterlengo, Italy. “The idea was to move from relying on images and 3D files to rapid prototyping machines and reduce our time to market,” explains Stefano Cademartiri, R&D, CAP and prototyping specialist at Unilever. “The new vision for the future of CAD development was to invest in a 3D printer that was easy to use and could produce fast concept prototypes using heat resistant ABS materials.”
Bu hikaye ET Polymers dergisinin Aug - Sept 2017 sayısından alınmıştır.
Start your 7-day Magzter GOLD free trial to access thousands of curated premium stories, and 9,000+ magazines and newspapers.
Already a subscriber ? Giriş Yap
Bu hikaye ET Polymers dergisinin Aug - Sept 2017 sayısından alınmıştır.
Start your 7-day Magzter GOLD free trial to access thousands of curated premium stories, and 9,000+ magazines and newspapers.
Already a subscriber? Giriş Yap
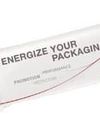
TotalEnergies and Jindal Films To introduce Certified Circular Polypropylene
TotalEnergies and Jindal Films have joined forces to produce more sustainable flexible food packaging and labels. Using advanced recycling technology from Plastic Energy, TotalEnergies will supply Jindal Films with Certified Circular Polypropylene produced from postconsumer plastic waste. This new value-chain collaboration will divert plastic waste currently destined for incineration and landfill because it is too complex to recycle through existing schemes.
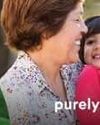
Lenzing's VEOCEL™ Brand Launches Hydrophobic Lyocell Fibres With Dry Technology
In its quest to drive greater sustainability in the personal care and hygiene industry, the VEOCEL™ brand has launched a new offering: VEOCEL™ branded lyocell fibres with dry technology which are naturally smooth and gentle on skin, ensuring comfort for sensitive skin. Absorbent hygiene products are an indispensable part of many consumers’ lives and are relied upon daily. As these are essential items, it is important that they should offer maximum comfort and relief to the user. This is demonstrated by the new VEOCEL™ branded lyocell fibres which have the capacity to provide a high level of comfort, softness and dryness, when applied in these types of products.
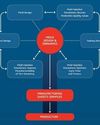
Simulating Injection Molding for Efficiency
Producing high-quality, plastic injection-moulded parts more quickly and cost-effectively has become a critical factor for manufacturing success in today’s global market. Instead of engaging in slow, expensive prototype iterations and test cycles to satisfy manufacturing requirements, designers, mold makers, and manufacturing professionals can leverage SOLIDWORKS® Plastics mold-filling simulation software to optimise parts for manufacturability, refine tooling to improve quality and shorten cycle times to reduce manufacturing costs

Perfecting your Purging Procedures
Determining the source of streaking or contamination in your molded parts is a critical step in perfecting your purging procedures, ultimately saving you time and money. We take a closer look at the nitty-gritty details of purging.
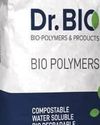
Going Sustainable With Polymers
Hi-Tech International is the first company in the country to manufacture a plantbased bio-polymer – Dr Bio – which can be used to replace single-use and multi-use plastic products with bio-compostable plastic. The Machinist take a closer look…
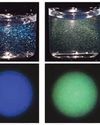
Inspired by Nature
A project researching the effects of structural colouration in nature and translating the same for pigmentation in industrial applications
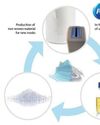
Face (mask) Off: Recycle & Reuse
Fraunhofer, SABIC, and Procter & Gamble join forces in a closed-loop recycling pilot project for single-use facemasks
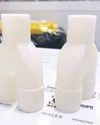
ELIX Polymers Joins The Fight Against Covid-19
Leading ABS producer ELIX Polymers is collaborating with a large group of companies within ClusterMAV, the Advanced Materials Cluster of Catalonia, Spain, in the fight against COVID-19.
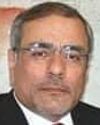
Investing in the Future
Umesh Anand, Managing Director, HPL Additives Limited talks to us about his company and its focus on innovation and sustainability
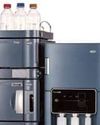
Waters Peptide Multi-Attribute Method for BioAccord System Boosts Innovator and Biosimilar Drug Development
Waters Corporation today introduced a new peptide multi-attribute method (MAM) workflow for the Waters™ BioAccord™ LC-MS System, enabling drug development, manufacturing, and QC scientists to monitor efficacy and safety through the analysis of critical quality attributes (CQAs) of monoclonal antibodies (mAbs) and other protein-based drugs.