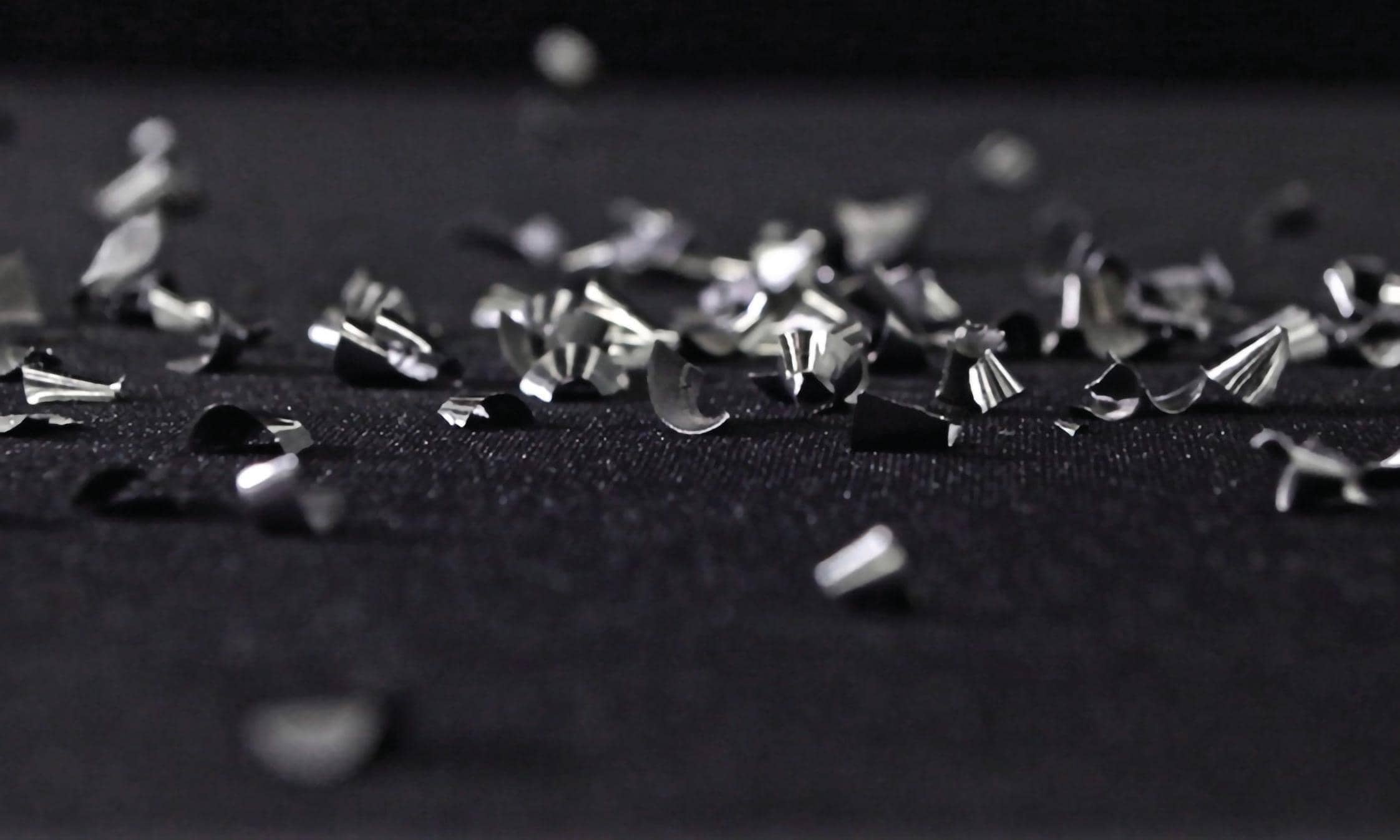
WHETHER EXAMINING HOW TOOL SELECTION impacts chips, how coolant plays a role in chip evacuation or the size and shape of chips, chip formation says a lot about the application being run. Knowing what different chip details indicate allows machinists to manage chip formation better, make adjustments and prevent tool failure. Because when it comes down to it, better chip formation means a more successful application.
SHAPE & SIZE
When looking at chip formation, a key indicator of a good chip is the shape. The preferred outcome for any application is chips shaped as sixes and nines or a single conical shape. These small, manageable chips are essential for efficient, predictable drilling. Nevertheless, it is important to be aware of what chips in other shapes and sizes can indicate. For example, a straight, flat chip is a result of elasticity. If the chip is a continuous ribbon, then there are likely many adjustments that need to be made in order to achieve ideal chips.
The size of the chips impacts evacuation as well. Two major factors impact the size of chips in drilling tools: chip breakers, also known as chip splitters, and lip geometry. With chip breakers, the width of the chip is thinned to allow for easier evacuation; the wider the chip, the easier it is to get it to roll onto itself and break. Lip geometry acts as a mechanical chip breaker to fracture a chip by curling the chip on top of itself or by impacting the chip forming with the backside of the lip radius. Although harder materials will curl a chip on top of itself to create chip fracture, gummier materials often skip over the lip radius and only fracture after impacting the back of the lip radius. Still, the purpose of the combined chip breakers and positive lip geometry is to break off the chip so that it is narrow enough to evacuate easily.
Bu hikaye Manufacturing Today dergisinin May 2022 sayısından alınmıştır.
Start your 7-day Magzter GOLD free trial to access thousands of curated premium stories, and 9,000+ magazines and newspapers.
Already a subscriber ? Giriş Yap
Bu hikaye Manufacturing Today dergisinin May 2022 sayısından alınmıştır.
Start your 7-day Magzter GOLD free trial to access thousands of curated premium stories, and 9,000+ magazines and newspapers.
Already a subscriber? Giriş Yap
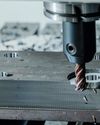
Optimising milling operations
Exploring innovative strategies that are reshaping the milling landscape to meet the challenges of a competitive global market.
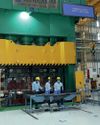
The path to excellence
Tata AutoComp’s Double Deming triumph is testament to quality and innovation
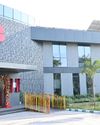
Boosting India's energy efficiency with advanced low voltage motors
Stefan Floeck, Division President of IEC Low Voltage Motors at ABB Motion, discusses the role of low voltage motors in India’s industrial future.
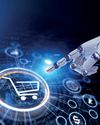
The Tech of E-commerce
Technology is revolutionising e-commerce by enhancing demand forecasting, inventory management, and customer experiences through AI, blockchain, IoT, and real-time data analytics.
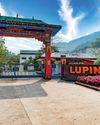
Driving Sustainability and Innovation
A conversation with Rajendra B Chunodkar, President Manufacturing Operations, Lupin
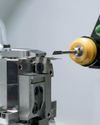
The evolution of machining technologies
The evolution of machining technologies is reshaping the manufacturing landscape, offering unprecedented opportunities for efficiency, precision, and sustainability.
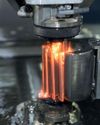
Transforming the future of manufacturing technology
A pre-event report on IMTEX 2025: The premier manufacturing and metal cutting technologies event for
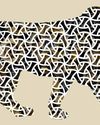
THE MAKE IN INDIA JOURNEY
An analysis of the initiative's impact on the manufacturing sector.
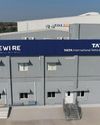
Tata Motors Re.Wi.Re: Innovation meets responsibility
Tata Motors advances circular economy via Re.Wi.Re scrapping facility.
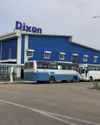
After Apple, Google Pixel set to be manufactured in India
Dixon Technologies' alliance with Compal Electronics is poised to further accelerate India's push to become a global hub for smartphone manufacturing.