CATEGORIES
Categorías
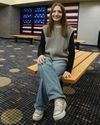
AI IS A GAME CHANGER FOR STUDENTS WITH DISABILITIES.SCHOOLS ARE STILL LEARNING TO HARNESS IT
For Makenzie Gilkison, spelling is such a struggle that a word like rhinoceros might come out as “rineanswsaurs” or sarcastic as “srkastik.”
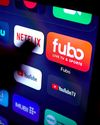
FUBO COMBINING WITH DISNEY'S HULU + LIVE TV; LAWSUIT AGAINST VENU SPORTS SETTLED
Disney's Hulu + Live TV and sports streaming service Fubo are combining in a deal that will also see the settlement of a lawsuit against the creation of Venu Sports.
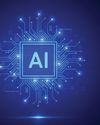
AI IS BECOMING INGRAINED IN BUSINESSES ACROSS INDUSTRIES.WHERE IS IT GOING IN 2025?
As artificial intelligence continues to grow at a rapid pace, more and more businesses are grappling with how to adapt both quickly and responsibly.
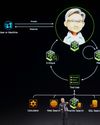
BIGGEST NVIDIA TAKEAWAYS FROM JENSEN HUANG'S CES 2025 KEYNOTE
Nvidia CEO Jensen Huang unveiled a suite of new products, services and partnerships at CES 2025. In a packed Las Vegas arena, Huang kicked off the CES this week with his vision for how his companies' products will drive gaming, robotics, personal computing and even self-driving vehicles forward.
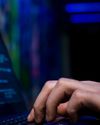
NEW LABELS WILL HELP PEOPLE PICK DEVICES LESS AT RISK OF HACKING
The federal government is rolling out a consumer labeling system designed to help Americans pick smart devices that are less vulnerable to hacking.
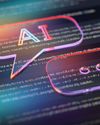
IN 2024, ARTIFICIAL INTELLIGENCE WAS ALL ABOUT PUTTING AI TOOLS TO WORK
If 2023 was a year of wonder about artificial intelligence, 2024 was the year to try to get that wonder to do something useful without breaking the bank.
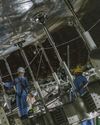
A NEW NEUTRINO DETECTOR IN CHINA AIMS TO SPOT MYSTERIOUS GHOST PARTICLES LURKING AROUND US
Underneath a granite hill in southern China, a massive detector is nearly complete that will sniff out the mysterious ghost particles lurking around us.
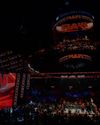
WWE READY TO BEGIN NETFLIX ERA WITH 'MONDAY NIGHT RAW' MOVING TO THE STREAMING PLATFORM
Nick Khan's prediction becomes a reality on Monday night.The World Wrestling Entertainment executive said during earning calls in the past that he saw a day when Netflix would continue to evolve and enter into live programming, much to the consternation of Netflix officials.However, Khan saw the hires that Netflix was making along with the streaming service's offerings that could appeal to all family members.
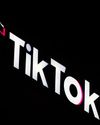
TIKTOK CREATORS LEFT IN LIMBO WHILE AWAITING DECISION ON POTENTIAL PLATFORM BAN
Will TikTok be banned this month?
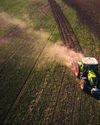
FARMING TECH IS ON DISPLAY AT CES AS COMPANIES SHOWCASE THEIR GREEN INNOVATIONS AND INITIATIVES
When Russell Maichel started growing almonds, walnuts and pistachios in the 1980s, he didn't own a cellphone. Now, a fully autonomous tractor drives through his expansive orchard, spraying pesticides and fertilizer to protect the trees that have for decades filled him with an immense sense of pride.
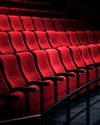
PARTICIPATE OR KEEP IT QUIET? RECENT SING-ALONGS TAP INTO LARGER DISCUSSION ON MOVIEGOING ETIQUETTE
As movie theaters worked to entice Americans back into seats after COVID-19 lockdowns and labor strikes, the industry marketed blockbuster films like “Wicked “and the dueling releases of “Barbie “and” Oppenheimer “as no less than cultural events.
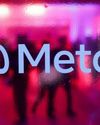
META TRIES LETTING FACEBOOK MARKETPLACE USERS VIEW EBAY LISTINGS AS WAY TO RESOLVE EU CHARGES
Meta said this week that it will allow some Facebook users to view eBay listings on its Marketplace service, as it tries out a possible way to resolve European Union charges of anticompetitive behavior that the bloc leveled last year.
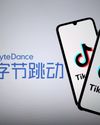
BYTEDANCE'S LEMON8 GAINS TRACTION AMID TIKTOK BAN THREAT AS CREATORS PUSH THE APP
Hearing a lot about Lemon8 lately? You're not the only one.
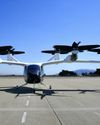
FLYING TAXIS ARE ON THE HORIZON AS AVIATION SOARS INTO A NEW FRONTIER
When he was still a boy making long, tedious trips between his school and his woodsy home in the mountains during the 1980s, JoeBen Bevirt began fantasizing about flying cars that could whisk him to his destination in a matter of minutes.
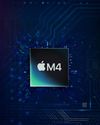
Macs Unified
THE M4 CHIP LINEUP WE'VE BEEN EXPECTING FOR OVER A DECADE
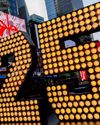
10 TIPS FROM EXPERTS TO HELP YOU CHANGE YOUR RELATIONSHIP WITH MONEY IN 2025
If you're planning to make financial resolutions for the new year, experts recommend that you start by evaluating the state of your finances in 2024. Then, set specific goals and make sure they're attainable for your lifestyle.Here are some tips from experts:
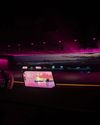
FROM AI ASSISTANTS TO HOLOGRAPHIC DISPLAYS, AUTOMAKERS SHOWCASE IN-CABIN EXPERIENCES AT CES
Interior lighting aimed at reducing motion sickness. Shiny holographic dashboards displayed on windshields. And Al-powered voice assistants paired with infotainment systems to keep you company on long drives.
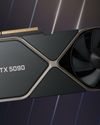
NVIDIA'S NEW GPU SERIES LED AN AVALANCHE OF ENTERTAINMENT-RELATED ANNOUNCEMENTS AT CES
In a packed Las Vegas arena, Nvidia founder Jensen Huang stood on stage and marveled over the crisp real-time computer graphics displayed on the screen behind him. He watched as a dark-haired woman walked through ornate gilded double doors and took in the rays of light that poured in through stained glass windows.
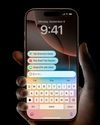
APPLE TO PAY $95 MILLION TO SETTLE LAWSUIT ACCUSING SIRI OF EAVESDROPPING
Apple has agreed to pay $95 million to settle a lawsuit accusing the privacy-minded company of deploying its virtual assistant Siri to eavesdrop on people using its iPhone and other trendy devices.
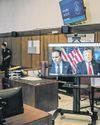
Trumps Begin Talks To Reclaim D.C. Hotel
Donald Trump's real-estate company is in talks to reclaim its former Washington, D.C., hotel, a move that could offer an early test of how the president-elect will handle potential conflicts of interest.
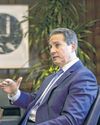
Fed Official Says Further Cuts Can Wait
Musalem suggests he favors greater caution in trimming interest rates more
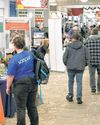
Jobs Growth Exceeds Expectations
Continued from Page One from Thursday's 4.68%. That was its highest in more than a year. The silver lining for markets was that wage growth contin- ued to moderate. Average hourly earnings rose 0.3% from November to $35.69, in line with expectations but slightly slower than the prior month. That leaves intact the Fed's the- sis that the labor market isn't a source of inflationary pressure.
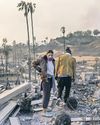
One L.A. Wildfire Swept Away A Rare Middle-Class Paradise
It was a sliver of paradise that people could actually afford, hidden along a coveted stretch of Southern California coastline.
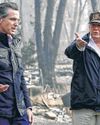
Trump to Inherit a Crisis In State He Has Scorned
President-elect Donald Trump's critiques of California have become a central part of his political brand. He has called the state \"crime-ridden,\" overrun with migrants and \"failing,\" and he frequently spars with the state's Democratic political leaders.
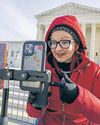
Justices Cast Doubt on TikTok's Fight Against Ban
The Chinese-owned app is battling for survival as a deadline looms over its fate
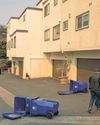
Against All Odds, Some Homes Are Spared
One corner of the Pacific Palisades is untouched amid Surrounding inferno
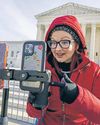
Justices Cast Doubt on TikTok's Fight Against Ban
The Chinese-owned app is battling for survival as a deadline looms over its fate TikTok seemed headed for shutdown after Supreme Court arguments Friday, where justices indicated strong support for the government's security concerns regarding the trove of personal data the Chinese-controlled app collects from nearly half the U.S. population.
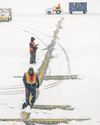
Winter Storm Grounds Thousands of Flights
A winter storm in the South brought heavy snowfall Friday, causing thousands of flight cancellations and several governors to declare states of emergency. More than 46 million people were under a winter storm warning Friday, with some areas expected to get more than a foot of snow, according to the National Weather Service. The storm disrupted daily life in the South, with local businesses and schools closed across the region.
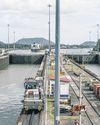
Panama Canal Threat Stirs a Nationalist Ire
Every year on Jan. 9, Panama's president lays a wreath next to an eternal flame near the canal that made this country prosperous. It is a memorial to the Panamanians killed by U.S. forces in 1964 riots over U.S. control of the canal.
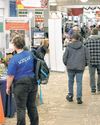
Jobs Growth Tops Expectations
Report puts further Fed rate cuts in doubt; stocks sell off, while yields rise