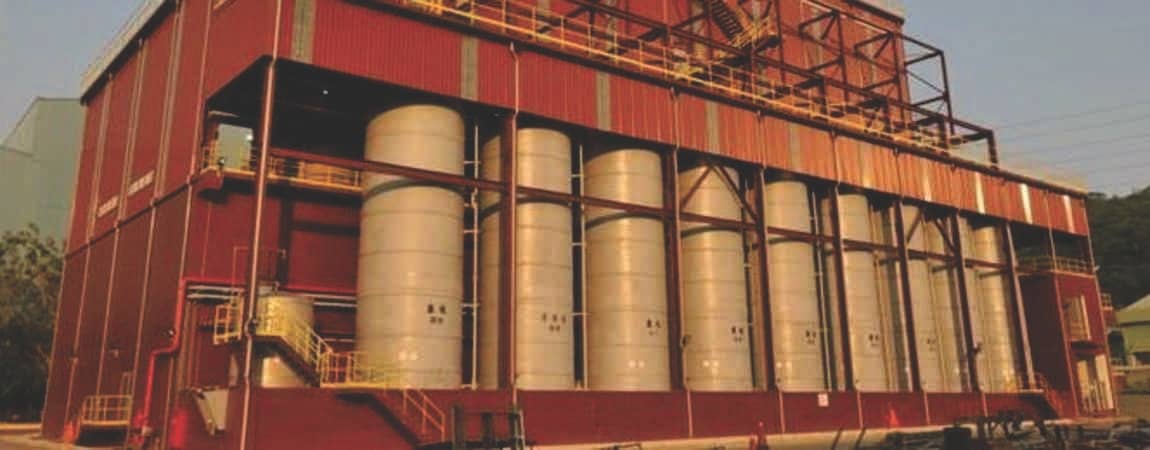
Steel manufacturing involves a range of interlinked chemical processes. The end product is a composite of successive stages of chemical pretreatment for removal of impurities, right from raw materials processing to rolling, pickling and color coating. Economies of scale call for a high level of operational efficiency and the aim of technological innovation is the valorisation of value – both in quantitative and qualitative terms.
Waste Acid: An Eco Hazard?
In steel mills, the hot rolled steel coil (HRC) requires pre-treatment before undergoing various other processes like cold rolling and galvanizing. Chemical pre-treatment is aimed at removing various oxide layers, rust or scale from the steel surface by passing the workpiece, as it is called, through a vat of pickle liquor. The pickling process generates large amounts of pickling sludge containing acidic rinse water, dissolved metal salts of iron, iron chloride, zinc and waste acid. The spent pickle liquor is considered hazardous waste and, therefore, environmental considerations – over and above economic concerns related to regeneration and reuse – stand in the way of instant disposal.
Pickling of carbon steel is a process in which a thin layer of oxidized iron, or scale, is removed from the surface of the steel. The reaction of alloying metals with oxygen at high temperatures during hot rolling leads to the formation of scales. Pickling involves placing the HRC on an uncoiler and the strip is pulled through the acid bath section, which comprises four tanks in a row containing hydrochloric acid, at a specific speed. The rubber scrubber scrubs the surface to remove the impurities. The strip is subsequently passed to a water tank where it is rinsed with water spray and air-dried, leaving a dull silver luster to the metal. At the end of the pickling line, the strips recoil.
Pickling Processes
Diese Geschichte stammt aus der January 2020-Ausgabe von Steel 360.
Starten Sie Ihre 7-tägige kostenlose Testversion von Magzter GOLD, um auf Tausende kuratierte Premium-Storys sowie über 8.000 Zeitschriften und Zeitungen zuzugreifen.
Bereits Abonnent ? Anmelden
Diese Geschichte stammt aus der January 2020-Ausgabe von Steel 360.
Starten Sie Ihre 7-tägige kostenlose Testversion von Magzter GOLD, um auf Tausende kuratierte Premium-Storys sowie über 8.000 Zeitschriften und Zeitungen zuzugreifen.
Bereits Abonnent? Anmelden
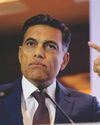
Sajjan Jindal's Pills For Steel Sector Ills
Making an impassioned cry for the entire steel industry to come forward and join hands to devise ways to increase steel consumption in India, Sajjan Jindal, Chairman of the JSW Group, recently said the USD 200-250 billion of investment that will be required to produce the 300 million tonnes (MnT) of steel by 2030 should be made in all “Make in India” equipment.
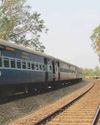
Galvanised Rails On Track To Be INR 1,400-CR Opportunity
If all goes well, Indian Railways (IR) could be having an INR 1,400-crore, 2 lakh tonnes per annum order for galvanised rails to offer one-and-half years down the line. And two leading producers of rail tracks in India, the Steel Authority of India (SAIL) and Jindal Steel & Power (JSPL), could be in the fray to bag the orders, it is learnt.
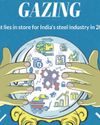
Crysteel Gazing
What lies in store for India's steel industry in 2020?
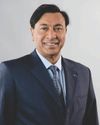
Are Indian Steel Makers Ready To Combat Arcelormittal's Arsenal?
Armed with deep pockets and the best available technology in its arsenal, the world’s largest steel maker, ArcelorMittal, is all geared up to own and steer an operating 10-million tonnes per annum (MnTPA) steel plant in India, and a growing market that offers an attractive opportunity for steel firms with excess capacity from China, Japan and Korea (more so for the last two, owing to favorable trade agreements) to dump products unbridled at predatory prices
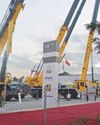
Construction Equipment Sector May See 40% Growth In Sales
The construction equipment industry can expect a 40% increase in sales in the near future on the back of huge government spending on infrastructure projects.
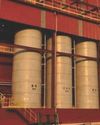
Acid Test
When it comes to spent pickle liquor, steel makers need to embrace innovative solutions to reduce environmental impact & increase efficiency
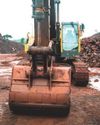
Stress On 'Scientific Mining': Odisha Mining Lease Area Cap Eased
But govt's decision keeps industry divided
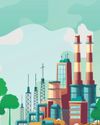
Let's Get Carbon-Smart
Innovations are inevitable for the global steel industry to ride over the myriad challenges that the worldwide environmental crisis has thrown up. And almost all the ground-breaking innovations in steel technology have been geared towards confronting and mitigating the carbon challenge. The singular objective of disruptive technologies is to become, what has been aptly termed as “carbon smart”, by not just replacing fossil sources with natural gases for metals production but also recycling fossils and wastes to produce useful products at an industrial scale, thereby providing a huge fillip to the global circular economy. Steel360 turns the spotlight on three “green” technologies that are setting new benchmarks in the industry.
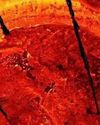
Loss Of Unreduced Slag Is A Direct Loss Of Iron
Improving EAF operations through monitoring and control of slag residence time
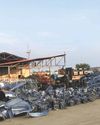
Auto Scrap Facility Draft Norms Drive Home ‘Green' Point
However, ambiguities keep stakeholders at crossroads