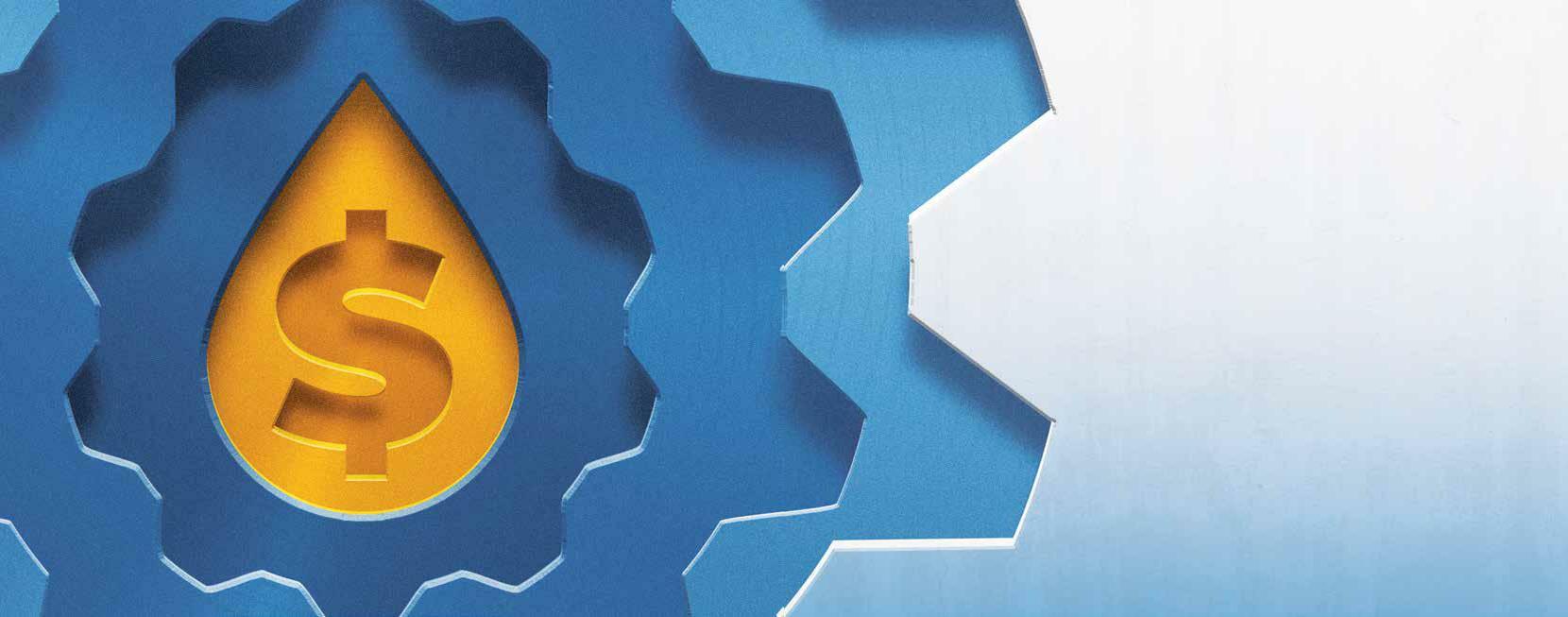
Being able to extend oil drains or even shorten them to eliminate failures can be an easy way to reduce maintenance costs, but data must be available that allows for making those decisions. This article will address the role of key performance indicators (KPIs) in predictive maintenance, how to gather useful data that aligns with KPIs and review a few case studies where onsite labs were able to use data to take advantage of warranty periods, justify keeping assets after warranty and extend the interval between oil drains to reduce oil consumption.
Oil Analysis Introduction
Lubricant analysis is much like a blood test for humans. By trending the correct parameters like blood pressure and cholesterol, the patient gains an understanding of overall health. Deviations in those trends over time indicate that action needs to be taken. The same concept can be applied to machinery health when looking at the three key areas of oil analysis: wear, contamination and chemistry. Using data in these three areas can lower overall maintenance costs, reduce unplanned downtime and increase asset life. Within a plant setting, oil analysis is often paired with several other technologies that encompass the Condition-based Maintenance (CBM) Program. The most common technology seen is vibration analysis. Typically, vibration analysis picks up on faults just a little bit later in the failure progression process than oil analysis, which is why they are typically paired together. Infrared thermography and motor circuit analysis are also used from time to time. Pairing technologies together gives confidence in the results and helps the engineer make critical decisions (if needed) to take a machine offline or remove it from service.
Esta historia es de la edición July/August 2023 Issue de MACHINERY LUBRICATION INDIA.
Comience su prueba gratuita de Magzter GOLD de 7 días para acceder a miles de historias premium seleccionadas y a más de 9,000 revistas y periódicos.
Ya eres suscriptor ? Conectar
Esta historia es de la edición July/August 2023 Issue de MACHINERY LUBRICATION INDIA.
Comience su prueba gratuita de Magzter GOLD de 7 días para acceder a miles de historias premium seleccionadas y a más de 9,000 revistas y periódicos.
Ya eres suscriptor? Conectar
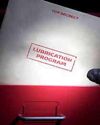
The Secrets For Implementing A Clean lubricant Program
If you could find an investment that guaranteed a return 40 times greater than your initial investment, you probably wouldn't pass it up.
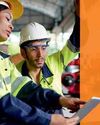
MAINTAIN? REPAIR? REPLACE?
When considering the life of any asset, the question arises: what types of interventions should be planned to keep it operating or to restore operation in the event of its failure?
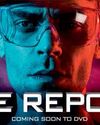
Engineering Reports Should Be Like Bad Movies
I'm frequently asked to review engineering reports, and I'm continually baffled by how many engineers want to take their readers on a journey instead of getting to the point.
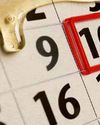
WHY SCHEDULED OIL CHANGES AREN'T ENOUGH TO MITIGATE LUBRICANT CONTAMINATION
There are few problems more insidious or damaging to large industrial machinery than contaminated lubricant.
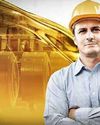
LUBRICATION CONTAMINATION PREVENTION
How many articles have you read, or seminars listened to, that tout the value of contamination control? If you are like me, they number in the hundreds—if not thousands. One thing about these articles and seminars that bothers me is the word “control”.
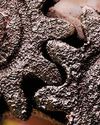
LUBRICANT CONTAMINATION PREVENTION AND MITIGATION: A Guide For Maintenance Professionals
Lubricants are essential for the smooth and efficient operation of many types of machinery, from engines and turbines to gears and bearings.
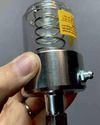
TASK-BASED TRAINING | INSPECTING A SINGLE-POINT LUBRICATOR
A single-point lubricator is a device engineered to attach to a single unit to regularly and automatically deliver a small amount of clean grease or lubricating oil to a specific area.
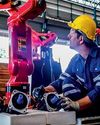
TOP LEADERSHIP FOCUSES FOR IMPROVED RELIABILITY AND COST REDUCTION
Here’s a scenario that may sound eerily familiar – you have a new reliability initiative.
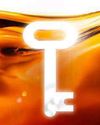
4 KEY ELEMENTS FOR INTERPRETING AN OIL ANALYSIS REPORT
Years ago, a customer came into my office, visibly upset. He had just received his second oil analysis report for one of his Caterpillar gas engines.
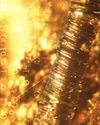
ASTM ENHANCEMENTS TO MICROSCOPIC PARTICLE IDENTIFICATION AND DOCUMENTATION
In 1982, Daniel Anderson published his influential book, \"Wear Particle Atlas\", which describes, sizes, and classifies particles found in oil.