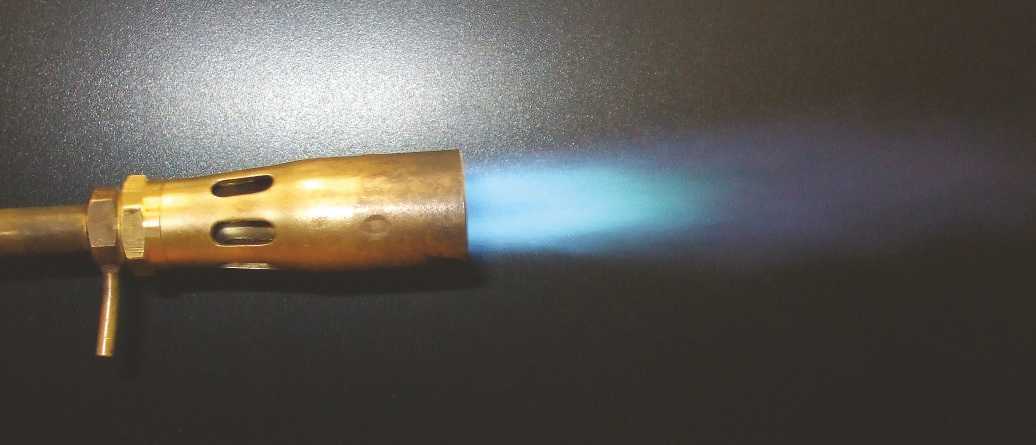
It is a common comment that some model engineers, although happy to braze copper, have difficulties when it comes to joining steel. The key to success for any brazing, or indeed soldering operation, is to embrace the basic principle – that of capillary flow. Let us be clear about one thing from the outset, brazing is a metal joining process which depends on capillary flow of molten metal between two closely adjacent surfaces. It has nothing to do with the filler metal. If you are not using capillary flow, you are not brazing.
Brazing is brazing whether you are using a silver solder or a brass rod.
The same principles that apply to joining copper with a silver solder are identical to those joining steel with a brass rod. The principles are independent of the material being used to make that joint. Any reader that fails to acknowledge this might just as well turn the page now!
However, it is fair to say that there are slightly different practicalities to be considered if you are to achieve the necessary capillary flow when brazing steel compared to copper.
The main difference lies in the heating technique when brazing steel.
Steels, and all ferrous materials, be they stainless, mild steel or cast iron, have a higher specific heat than copper. It takes more energy (heat) to raise 1gm of steel by 1°C than it does to achieve the same effect for copper. The values for copper and steel are shown below.
Copper 0.38J/gm-°C Steel 0.51J/gm-°C
This means that for any given torch,
it requires 25% more heat and will take nearly 25% longer to achieve the brazing temperature. So be patient!
Denne historien er fra December 2019-utgaven av Model Engineers' Workshop.
Start din 7-dagers gratis prøveperiode på Magzter GOLD for å få tilgang til tusenvis av utvalgte premiumhistorier og 9000+ magasiner og aviser.
Allerede abonnent ? Logg på
Denne historien er fra December 2019-utgaven av Model Engineers' Workshop.
Start din 7-dagers gratis prøveperiode på Magzter GOLD for å få tilgang til tusenvis av utvalgte premiumhistorier og 9000+ magasiner og aviser.
Allerede abonnent? Logg på

Readers' Workshops - Patrick Cubbon
Patrick Cubbon describes his workshops – a portable one from 1963 and the current accommodation

Desktop Gear Hobbing
Toby Kinsey has designed this fascinating piece of gearmaking equipment

The John Stevenson Trophy 2020
Many readers and forum members will remember John Stevenson, a contributor to MEW but best known for his larger-than life presence on the Model Engineer forum.

From the Archives: Twist drill Sharpening by the Four Facet Method
Giles Parkes, MEW Issue 64, February/March 2000

Dividing on the Warco 220 Lathe
Peter Shaw describes a mandrel dividing attachment for this popular lathe that can be adapted to fit many other benchtop machines

Choosing Steels
Stub Mandrel offers some advice on choosing the right steel for the job

A Storage Story
Robin King shares the lessons learned from his experience of workshop moves

A Simple Drill Grinding Aid
A newcomer to our hobby was having trouble sharpening drills, so Howard Lewis made a simple aid for him

Yet Another Bodge-Up!
Peter Shaw finds a use for some aged homebrew slot drills.

Workshop Press Tooling Part 2
Will Doggett makes a set of tooling for his press tool described starting in issue 285