CATEGORIES
Kategorier
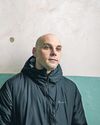
Ukrainian Ex-POWs Survived Torture at Hands of Russians
Twenty-six Ukrainian prisoners of war sat naked on a cold stone floor, their legs crossed, heads bowed and hands clasped behind their backs.
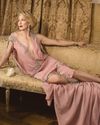
NOW YOU SEE HER
Bertha Russell would be so disappointed. When Carrie Coon, who plays the calculating social climber on The Gilded Age, sits down at the Regency Bar & Grill, just a few blocks and about 140 years from the fictional mansion where her character resides, it's the tail end of the restaurant's infamous power breakfast—a crucial error in timing for anyone hoping to rub elbows with New York City's ruling class.
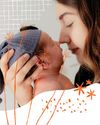
The Sacredness of Human Development
CHRISTIANNA DEICHMANN is the Director of Education at the Association for Prenatal and Perinatal Psychology and Health (APPPAH), where she educates both professionals and parents on fostering the most nurturing environments for welcoming new life into the world. She is based in Charlottesville, Virginia, USA. With a multidisciplinary approach, Christianna blends Craniosacral Therapy, massage, and pre- and perinatal psychology into her holistic practice. Her work uniquely combines science and spirituality.In part 2 of this interview, Christianna continues to shares her expertise with DR. SNEHAL DESHPANDE, a Developmental Therapist, PPNE, and the Director of Heartfulness Family Connect Programs, offering a rich dialogue on Birth Trauma and Obstetrical Intervention.
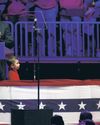
Musk Criticizes AI Project Backed By Trump
President's close ally raises questions on funding, spars online with OpenAI chief
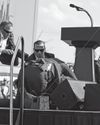
The Secret Service and the President's Life
The week Donald Trump won re-election, the Justice Department warned about continued assassination plots against elected officials, this time from Iran.
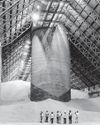
Rising Corn Prices Offer Growers Hope
However, Trump's tariffs could quickly halt gains and demand for the grain
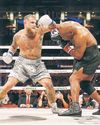
Netflix Explodes Into a New Era
Streamer unveils blowout subscriber numbers and price increase, but record value sets a high bar
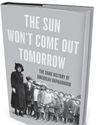
Children Who Need Parents
The Sun Won't Come Out Tomorrow
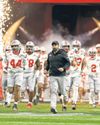
The Most Valuable Program In College Football Is Ohio State
OHIO STATE just won the right to call itself college football's national champions by stomping Notre Dame. But even before they took down the Fighting Irish, the Buckeyes had already earned an even more lucrative title.
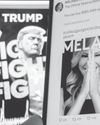
Meme Coins Like Trump's Stir Wild Market
Just days ahead of his return to the White House, President Trump and his wife, Melania, launched a pair of meme coins that have skyrocketed in value and earned them billions of dollars, at least on paper.
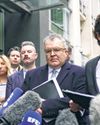
Prince Harry Settles U.K. Tabloid Suit
Murdoch's papers apologize for privacy intrusions on Duke and Princess Diana
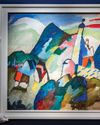
WHERE THE WILDLY EXPENSIVE THINGS ARE
In a small city in the Dutch hinterlands, sharp-elbowed dealers hunt the biggest game of all: billionaire collectors voracious for treasures from the last art fair that truly matters.
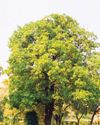
The Devil's Tree
DR V. RAMAKANTHA, retired forest officer, who lived, raised a family, and worked in forests for most of his adult life, returns to our pages in 2025 to share his vast knowledge of medicinal plants, and the fascinating stories associated with them. In his signature style, this month he weaves together science, folklore, and traditional knowledge to tell the story of the Devil's Tree, Saptaparni.

ONCE UPON A Saturday
SULOCHANA SANTHOSH is a young and inspired writer who reminds us of the need to care for our ocean and the environment in general. What are you doing to make a difference?
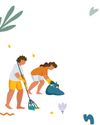
Seven of Us
is a lecturer at the Bangkok School of Management, a wellness coach, and the co-leader of the Bangkok Women's Writers Group. Here, Bhavna writes about her inspiring experience of cleaning up the garbage in the city that is her home.
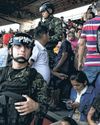
Drug Violence Surges in Colombia
The war over cocaine between armed groups in northeastern Colombia has killed about 80 people in recent days and forced tens of thousands to flee their homes, signaling a likely end to President Gustavo Petro's plans to sign peace accords with drug-trafficking groups.
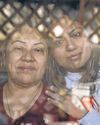
Not Just Homes, but Also Many Workplaces, Have Vanished
LOS ANGELES-Antonieta Lopez knew each feature and quirk of the stately, East Coast-style home on Villa View Drive.
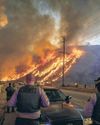
New Wildfire Spreads Quickly In L.A. County
Hughes fire scorches thousands of acres north of Santa Clarita, forces evacuations
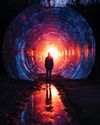
UNLEASHING OUR Extraordinary Capabilities
LYNNE McTAGGART is one of the central authorities on the new science of consciousness, and the award-winning author of seven books, including the internationally bestselling The Intention Experiment, The Field, The Bond, and The Power of Eight. Here, Lynne is interviewed by PURNIMA RAMAKRISHNAN about the transformative power of intention, the profound impact of group intention, and the potential for individuals to create significant change in their lives and the world.
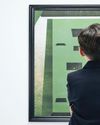
How Young Is Too Young to Start an Art Collection?
It will take more than just a trust fund to get them to sell you that painting.
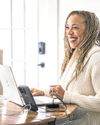
Baby-Boomer Women Power Wealth Transfer
They now have the final say on how family nest eggs get parceled out
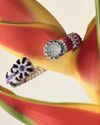
Give Me Liberty!
Creative freedom, it turns out, is a very wise investment.
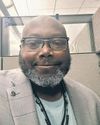
President Begins to Dismantle And Reshape Federal Workforce
President Trump's pledge to upend the federal workforce began rippling through Washington after he moved to force government employees back to the office five days a week, weakened their job protections and froze diversity efforts across the government.
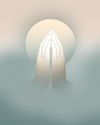
The Beauty and Transformative Nature of Prayer
In the first episode for 2025 on spiritual practices, DAAJI offers us an inspiring and scientific explanation of prayer and its importance on the inner journey. He demystifies prayer by going beyond the religious connotations to its true purpose and the benefits it offers us as a means of evolution.
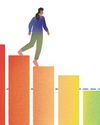
FROM Annoyance Serenity ΤΟ
SARALA UPADHYA shares her experience as a college professor to come up with a working model for how to manage annoyance both usefully and kindly. She has now reduced her “annoyance factor” making life more serene for herself and those around her.
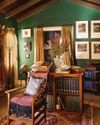
READ THE FINE PRINT
Nestled among the winding, narrow streets of Berkeley, California, which curve past a pastiche of architectural styles, including the material opulence of the spare modern mansions belonging to the tech elite, Susan Filter and Peter Koch's home stands apart.
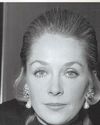
The ROTHSCHILD and the SNOWSTORM
Four decades after Jeannette May's remains were found on an Italian mountainside, the authorities have reopened the investigation into who or what-killed the former Lady de Rothschild.Was it a kidnapping? A mafia hit? Or have the rumors been wrong all along?
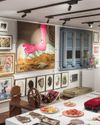
THE MASTER BUILDER
For the collector and philanthropist Amalia Amoedo, living with art and supporting the people who make it isn't just a choice it's a tradition. Is it any wonder she's known as Latin America's Peggy Guggenheim?
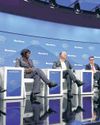
Davos Dissects Risks, Rewards of Trump
Bankers, government officials see benefits tilting toward U.S, away from Europe
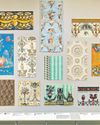
A Passion for Patterns
An exhibition highlights the fragile beauty and striking designs of centuries-old wallpaper