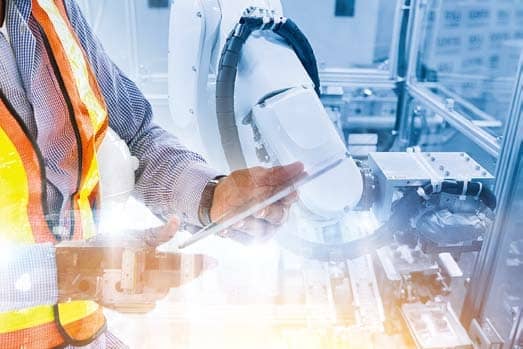
For plant managers however, downtime is a word that triggers concerns about lost production and lower revenue. That’s especially true for unplanned downtime and there is growing evidence that manufacturers are still unaware of the full impact of the problem. Automation parts supplier, EU Automation (euautomation.com), assesses some of the latest research on manufacturer downtime and the steps manufacturers are taking to address the problem.
A recent report from Senseye based on data from 72 major multinational industrial and manufacturing companies has revealed that cumulatively, Fortune Global 500 companies lose a total of 3.3 million hours per year due to unplanned downtime. The True Cost of Downtime report also found that the average plant in its survey lost US$172 million to unplanned downtime, every year.
The cost of downtime in manufacturing
Accurately calculating downtime costs is a difficult task. Firstly, we need to recognise there are both tangible costs, such as the financial costs arising from lost production, as well as intangible costs such as erosion of customer trust or increased likelihood of workplace accidents. Any financial calculations about the cost of downtime are likely underestimating the true overall cost to manufacturers by ignoring these less obvious and immediate effects.
Secondly, there has until recently been a lack of reliable data upon which to base our judgements. Historically, plant managers relied mostly on human judgement. Nowadays, with the growing availability of connected sensors and data analytics software, a clearer picture is emerging. What is being shown quite consistently in many of these reports, of which The True Cost of Downtime is but the latest, is that when objective data is used as the basis for calculating downtime, the cost is higher than previously imagined.
This story is from the December 2021 edition of International Plastics News for Asia.
Start your 7-day Magzter GOLD free trial to access thousands of curated premium stories, and 9,000+ magazines and newspapers.
Already a subscriber ? Sign In
This story is from the December 2021 edition of International Plastics News for Asia.
Start your 7-day Magzter GOLD free trial to access thousands of curated premium stories, and 9,000+ magazines and newspapers.
Already a subscriber? Sign In
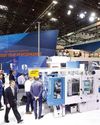
Industry innovations aimed towards a greener future
Sustainability and circular economy, energy saving technologies, high-performance materials with enhanced properties, and cost-efficient production processes are expected to dominate the plastics industry in 2022 and beyond.
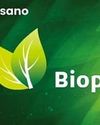
Special extrusion lines for bioplastic compounds
The biodegradable and compostable plastics sector is growing steadily, and this is partly due to the fact that several measures have been taken, especially in the EU, to cut down on single-use plastics.
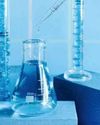
Plastics revolutionise medical device production
The coronavirus pandemic has brought into focus the urgent need for medical supplies – which included medical disposables, medical devices, laboratory equipment, and many others.
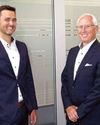
Spinning and recycling go together in a single step
As a medium-sized German machine construction business, BB Engineering has been manufacturing components and systems for synthetic fibre and film production for more than 20 years.
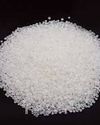
Advanced high-performance light stabilisers
A range of high-performance light stabilisers with enhanced properties are now being made available.
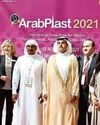
ArabPlast holds successful edition
The 15th Edition of ArabPlast was held on 15-18November 2021 at the Dubai World Trade Centre, Dubai, U.A.E. Spanning over 28 years, ArabPlast is an exclusive event for plastics, petrochemicals, packaging and rubber industry, and serves as an attractive platform where global industry players show off their products to the Middle East market.
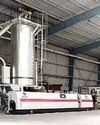
Food-grade plastics recycling facility installed in India
The well-established Indian recycler commissioned a PET bottle-to-bottle and a post-consumer polyolefin recycling line from Starlinger in mid-September.
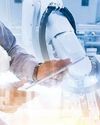
How to bring down downtime in manufacturing
For most of us, the word downtime conjures images of relaxation.
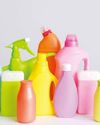
Optimistic forecast for blow moulded plastics market
Growing demand from key applications is a key factor in the projected growth of the blow moulding sector.
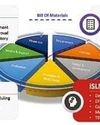
The benefits of dedicated system for mould development
When it comes to useful tools that can enhance teamwork efficiency, we usually think of the Product Lifecycle Management (PLM) systems.