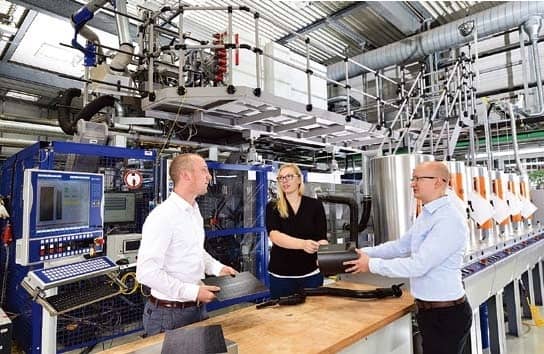
LANXESS is expanding the range of applications of extrusion blow moulding by facilitating the integration of its continuous fibre-reinforced thermoplastic composites under the Tepex brand into the production process. In a feasibility study, experts at the specialty chemicals company demonstrated that components made of polyamide 6 can be manufactured with blow moulding technology while receiving local reinforcement with Tepex at points subject to heavy loads. The investigations were performed on a state-of-the-art and close-toproduction blow moulding machine at the technical centre of the High Performance Materials business unit (HPM) in Dormagen. “The components show an outstanding adhesion, which allows utilisation of Tepex’s tremendous strength and rigidity,” explains Arthur Rieb, blow moulding specialist at HPM.
The process can be used to locally boost the mechanical performance of blow-moulded components, for instance in areas that are subject to high mechanical stress due to impact loads or high pressure. “In addition, it is suitable for the manufacture of blow-moulded structural components, for example hollow sections for car body reinforcement. Extensive use of Tepex can be a key factor in reducing weight and material use because the basic wall thickness of the component can be decreased,” Mr. Rieb explains. Based purely on thermoplastic systems, the hollow parts are easy to recycle, thus making it easier to establish closed-loop material cycles.
Simplified process
This story is from the October 2020 edition of International Plastics News for Asia.
Start your 7-day Magzter GOLD free trial to access thousands of curated premium stories, and 9,000+ magazines and newspapers.
Already a subscriber ? Sign In
This story is from the October 2020 edition of International Plastics News for Asia.
Start your 7-day Magzter GOLD free trial to access thousands of curated premium stories, and 9,000+ magazines and newspapers.
Already a subscriber? Sign In
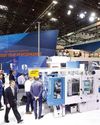
Industry innovations aimed towards a greener future
Sustainability and circular economy, energy saving technologies, high-performance materials with enhanced properties, and cost-efficient production processes are expected to dominate the plastics industry in 2022 and beyond.
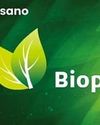
Special extrusion lines for bioplastic compounds
The biodegradable and compostable plastics sector is growing steadily, and this is partly due to the fact that several measures have been taken, especially in the EU, to cut down on single-use plastics.
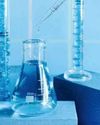
Plastics revolutionise medical device production
The coronavirus pandemic has brought into focus the urgent need for medical supplies – which included medical disposables, medical devices, laboratory equipment, and many others.
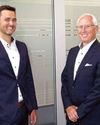
Spinning and recycling go together in a single step
As a medium-sized German machine construction business, BB Engineering has been manufacturing components and systems for synthetic fibre and film production for more than 20 years.
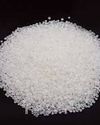
Advanced high-performance light stabilisers
A range of high-performance light stabilisers with enhanced properties are now being made available.
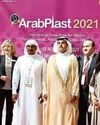
ArabPlast holds successful edition
The 15th Edition of ArabPlast was held on 15-18November 2021 at the Dubai World Trade Centre, Dubai, U.A.E. Spanning over 28 years, ArabPlast is an exclusive event for plastics, petrochemicals, packaging and rubber industry, and serves as an attractive platform where global industry players show off their products to the Middle East market.
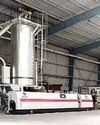
Food-grade plastics recycling facility installed in India
The well-established Indian recycler commissioned a PET bottle-to-bottle and a post-consumer polyolefin recycling line from Starlinger in mid-September.
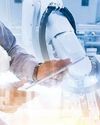
How to bring down downtime in manufacturing
For most of us, the word downtime conjures images of relaxation.
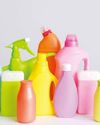
Optimistic forecast for blow moulded plastics market
Growing demand from key applications is a key factor in the projected growth of the blow moulding sector.
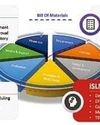
The benefits of dedicated system for mould development
When it comes to useful tools that can enhance teamwork efficiency, we usually think of the Product Lifecycle Management (PLM) systems.