CATEGORIES
Kategoriler
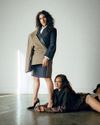
Don't Try This at Home
Comedians Kate Berlant and Jacqueline Novak are searching for their health holy grails-while trying not to fall for the bogus MAHA stuff.
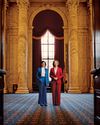
A 'Bright Spot' in Washington
Senators Angela Alsobrooks and Lisa Blunt Rochester aren't going to let that other election result prevent them from making history.
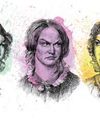
Sisterhood, Interrupted
Online, going \"no contact\" is often seen as liberating, empowering. If only I felt that way.
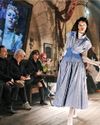
"I Wish More Designers Had That - a Real and Specific Sense of How They Want a Woman to Dress in 2025"
TEN YEARS OF FASHION: A Conversation Between CATHY HORYN and LINDSAY PEOPLES
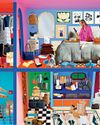
Do These Dupes Make Me Look Rich? AT QUINCE, THE ANSWER IS ALWAYS “YES."
How a one-stop shop for everything from cashmere sweaters to caviar seduced a generation of jaded shoppers.
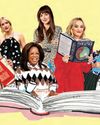
Which Celebrity Book Club Could (Actually) Change Your Life?
In the beginning, there was Oprah. Now, there are over a dozen celebrity-helmed book clubs that could make an author's career. But do they actually move the needle? \"It used to be that if you got a big book-club pick, your book was an automatic best seller, and that is so not the case anymore,\" says one publicist. We asked 15 authors and industry insiders what these clubs can really do for a book.
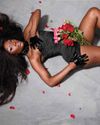
BOW DOWN TO DOECHII
Fresh off her Grammy win, the unapologetic Florida rapper is just getting started.
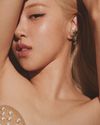
Confessions of a K-рор Star
For ROSÉ, writing her debut solo album was a form of therapy.
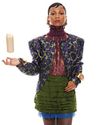
AT THEIR LEISURE...
FUN CLOTHES belong on FUN PEOPLE. So in NEW YORK and LOS ANGELES, we brought together 11 of our FAVORITE FOLLOWS, including the TIKTOK CELEBRITIES, ARTISTS, and MUSICIANS who are ALWAYS IN OUR FEEDS and on OUR MINDS, to talk about their secret (AND SOME NOT-SO-SECRET) PASSIONS and GUILTY PLEASURES. Who are they when NOBODY'S WATCHING?
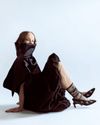
This Is Getting Interesting
The accessories are especially covetable this spring: futuristic sunglasses from Prada, lively little bags from Louis Vuitton, embellished socks from Fendi, and bejeweled headpieces from Valentino. Street-style darling Chloe King shared her tips for piling them on without going overboard.
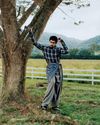
BIENVENIDO A BAD, BUNNY'S PUERTO RICO
BENITO ANTONIO MARTINEZ OCASIO's new album is a history lesson and a homecoming.
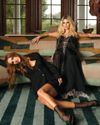
THE JESSICA & ASHLEE SHOW
One Simpson followed the rules, the OTHER BROKE THEM. Now, for the first entry in the Cut's \"Family Album\" series, JESSICA SIMPSON tells ASHLEE SIMPSON ROSS she's TAKING NOTES from her younger sister and refusing to let \"MEN IN SUITS\" boss her around.

GONE OFF THE GRID
In December, a fervent nationwide search for Hannah Kobayashi ended a 30-year-old named declared that she wasn't abruptly after police a missing person at all. The internet sleuths weren't satisfied.
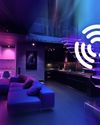
Proxima NEW BLUETOOTH & WI-FI TECH TO RESHAPE THE WIRELESS INDUSTRY
Apple has consistently pushed the envelope in terms of innovation, working to reduce its reliance on third-party suppliers while continuing to develop robust, energy-efficient devices.
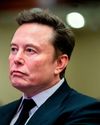
MUSK SAYS HE'LL WITHDRAW $97.4 BILLION BID FOR OPENAI IF CHATGPT MAKER REMAINS NONPROFIT
Elon Musk says he will abandon his $97.4 billion offer to buy the nonprofit behind OpenAI if the ChatGPT maker drops its plan to convert into a for-profit company.
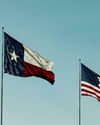
TEXAS COUNTY APPROVES HOLDING ELECTION TO MAKE SPACEX'S STARBASE ITS OWN CITY
A Texas county on Wednesday approved holding an election sought by SpaceX that would let residents living around billionaire Elon Musk ‘s company decide whether to formally create a new city called Starbase.
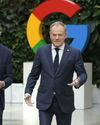
GOOGLE HUB IN POLAND TO DEVELOP AI USE IN ENERGY AND CYBERSECURITY SECTORS
Google and Poland on Thursday signed a memorandum for developing the use of artificial intelligence in the country’s energy, cybersecurity and other sectors.
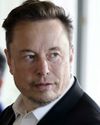
HOW ELON MUSK $97.4 BILLION BID COMPLICATES MATTERS FOR OPENAL
OpenAI CEO Sam Altman has dismissed a $97.4 billion takeover bid led by rival Elon Musk, but the unsolicited offer could complicate Altman's push to transform the maker of ChatGPT into a for-profit company.

SEC REQUESTS A PAUSE IN LEGAL BATTLE WITH BINANCE AS THE AGENCY ADAPTS A CRYPTO-FRIENDLY STANCE
The U.S. Securities and Exchange Commission is seeking to pause its high-profile lawsuit against the cryptocurrency exchange Binance as the regulator tries to present itself as more cryptofriendly under a new administration.
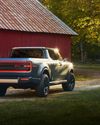
EV MAKER SCOUT MOTORS WANTS TO SELL DIRECTLY TO BUYERS BUT CAN'T DO IT IN ITS HOME STATE
Volkswagen-backed Scout Motors is making a massive bet in the electric SUV market with a carefully cultivated experience that will allow some customers to buy the company’s vehicle in minutes on an app and then use it to handle everything after from repairs to updates and upgrades.
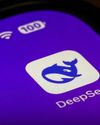
HOUSE LAWMAKERS PUSH TO BAN AI APP DEEPSEEK FROM US GOVERNMENT DEVICES
A bipartisan duo in the U.S. House is proposing legislation to ban the Chinese artificial intelligence app DeepSeek from federal devices, similar to the policy already in place for the popular social media platform TikTok.
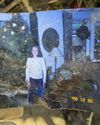
HOW PHOTOS LOST IN AMERICAN DISASTERS FIND THEIR WAY HOME, WITH A LITTLE HELP FROM PEOPLE WHO CARE
Hollowed-out homes. Cars entombed by mud. Unpeopled roads. Belongings reduced to dirt and debris.
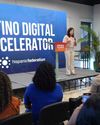
LATINO WORKERS WORKING TO OVERCOME A TECHNOLOGICAL DIVIDE BROUGHT ON BY AUTOMATION AND AI
As jobs become more reliant on technology some Latino workers can be left behind due to a lack of digital skills exacerbated by a lack of accessibility.
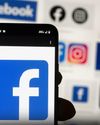
LOOKING FOR LOVE THIS VALENTINE'S DAY? DON'T FALL FOR INSTAGRAM ROMANCE SCAMS
If your social media suitor seems too good to be true, it might be a scam.
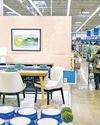
Can Walmart Keep The Retail Crown?
America's largest retailer is catching up quickly to Costco and Amazon. Now it needs to keep going.
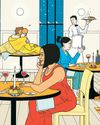
Don't Touch, Don't Go Dutch and Other Tips For Dating Success
Forget falling in love at first sight. A professional matchmaker offers some advice for a lasting relationship.
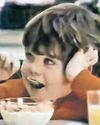
No, Pop Rocks Did Not Kill Mikey From The Life Cereal Ad
Before the internet, we amused ourselves with weird candy and outlandish rumors, spread person to person.
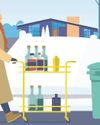
If I'm Sober-Curious, Do I Have to Toss My Bar Cart?
I don’t want mine to have anew purpose as toy storage or a flower cart.
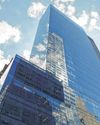
Hedge-Fund Investors Can't Cash Out
Armistice Capital delivered the goods to investors for over a dozen years. The hedge fund outperformed rivals in 2024, and its record since inception trounces the broader stock market.
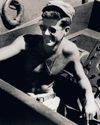
In the Crucible of Combat
Among the millions of World War II veterans were several future presidents. A few narrowly survived the experience.