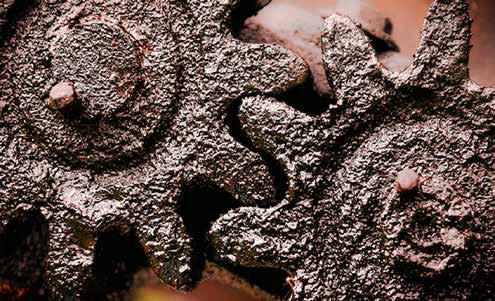
However, lubricants can also be vulnerable to contamination from various sources, such as dirt, dust, water, metal particles, microbes, and chemicals. Contamination can degrade the quality and performance of lubricants, leading to increased wear, friction, corrosion, oxidation, and varnish formation in the machines. This can result in:
• Reduced efficiency
• Increased downtime
• Higher maintenance costs
• Shorter equipment lifespan
The importance of lubricant contamination control – both prevention and mitigation – often goes unnoticed, despite the substantial financial and operational repercussions it holds. It is crucial for maintenance professionals to understand the importance of lubricant contamination control in operations. You can expect this article to discuss the definition and costs associated with lubricant contamination, as well as preventative maintenance strategies for various environments.
Definition of Contamination Control in Lubrication
Contamination control in lubrication is the process of minimizing or eliminating the ingress, generation, and accumulation of contaminants in lubricants and lubricated systems. Contaminants can be classified into three categories:
- Particulate
- 2. Liquid
- 3. Gaseous
هذه القصة مأخوذة من طبعة March - April 2024 من MACHINERY LUBRICATION INDIA.
ابدأ النسخة التجريبية المجانية من Magzter GOLD لمدة 7 أيام للوصول إلى آلاف القصص المتميزة المنسقة وأكثر من 9,000 مجلة وصحيفة.
بالفعل مشترك ? تسجيل الدخول
هذه القصة مأخوذة من طبعة March - April 2024 من MACHINERY LUBRICATION INDIA.
ابدأ النسخة التجريبية المجانية من Magzter GOLD لمدة 7 أيام للوصول إلى آلاف القصص المتميزة المنسقة وأكثر من 9,000 مجلة وصحيفة.
بالفعل مشترك? تسجيل الدخول
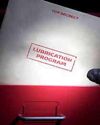
The Secrets For Implementing A Clean lubricant Program
If you could find an investment that guaranteed a return 40 times greater than your initial investment, you probably wouldn't pass it up.
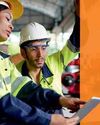
MAINTAIN? REPAIR? REPLACE?
When considering the life of any asset, the question arises: what types of interventions should be planned to keep it operating or to restore operation in the event of its failure?
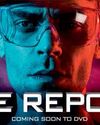
Engineering Reports Should Be Like Bad Movies
I'm frequently asked to review engineering reports, and I'm continually baffled by how many engineers want to take their readers on a journey instead of getting to the point.
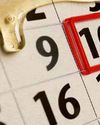
WHY SCHEDULED OIL CHANGES AREN'T ENOUGH TO MITIGATE LUBRICANT CONTAMINATION
There are few problems more insidious or damaging to large industrial machinery than contaminated lubricant.
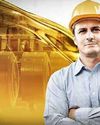
LUBRICATION CONTAMINATION PREVENTION
How many articles have you read, or seminars listened to, that tout the value of contamination control? If you are like me, they number in the hundreds—if not thousands. One thing about these articles and seminars that bothers me is the word “control”.
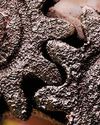
LUBRICANT CONTAMINATION PREVENTION AND MITIGATION: A Guide For Maintenance Professionals
Lubricants are essential for the smooth and efficient operation of many types of machinery, from engines and turbines to gears and bearings.
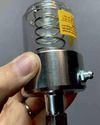
TASK-BASED TRAINING | INSPECTING A SINGLE-POINT LUBRICATOR
A single-point lubricator is a device engineered to attach to a single unit to regularly and automatically deliver a small amount of clean grease or lubricating oil to a specific area.
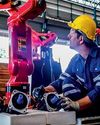
TOP LEADERSHIP FOCUSES FOR IMPROVED RELIABILITY AND COST REDUCTION
Here’s a scenario that may sound eerily familiar – you have a new reliability initiative.
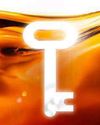
4 KEY ELEMENTS FOR INTERPRETING AN OIL ANALYSIS REPORT
Years ago, a customer came into my office, visibly upset. He had just received his second oil analysis report for one of his Caterpillar gas engines.
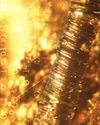
ASTM ENHANCEMENTS TO MICROSCOPIC PARTICLE IDENTIFICATION AND DOCUMENTATION
In 1982, Daniel Anderson published his influential book, \"Wear Particle Atlas\", which describes, sizes, and classifies particles found in oil.